In recent conversations with auto manufacturers, 48-V low-voltage rail has come up frequently. But why now? 48-V automotive systems aren’t new. They’ve helped improve efficiency and performance in mild hybrid electric vehicles (MHEVs) for years.
The renewed interest in 48-V systems might have to do with the growing popularity of both battery-electric vehicles (BEVs) and hybrid vehicles (HEVs). Electric or hybrid vehicles generating 48 V off a high-voltage battery can realize an important benefit of 48-V systems. Adding a 48-V low-voltage rail reduces the gauge of the wire harness that supplies power throughout the vehicle and reduces the load-current requirements of downstream semiconductor components, such as power switches and motor drivers. Thus, 48-V systems can deliver more power than 12-V systems, opening up the opportunity to add features that range from artificial intelligence to mini-fridges.
Government regulations and tax incentives are helping accelerate the shift to BEVs. To meet government requirements and improve the customer experience, BEV original equipment manufacturers (OEMs) are looking to optimize cost, weight and driving range. From an electrical perspective, it’s possible to address all three by reducing wire harnesses through a zone architecture or using a 48-V low-voltage rail for power distribution.
In the early 1900s, the automotive industry used a 6-V rail to provide power, until the power demands of the electrical/electronic (E/E) systems forced the market to move to 12 V. Now, today’s feature-rich vehicles are pushing the limits of 12-V rails, driving automakers to 48 V, which raises challenges but also opportunities.
48 V in MHEVs vs. BEVs
In the late 1990s, there was a push for 42-V E/E systems. But OEMs abandoned this approach given the lack of high-efficiency motors, and there was a market shift toward MHEVs that used a high-voltage starter generator. While MHEVs were the “first” 48-V systems, they used only a 48-V battery and a small electric motor to assist the internal-combustion engine, which reduced fuel consumption and improved efficiency.
The main low-voltage rail powering E/E systems in MHEVs remains at 12 V and requires a large bidirectional converter between the 48-V and 12-V rail, adding a large cost burden. In contrast, HEVs, plug-in hybrid vehicles (PHEVs) and BEVs can use the high-voltage battery to create a 48-V low-voltage rail to power the entire E/E system.
Because of limited trim lines and platforms, future BEV platforms were the primary target for OEMs to implement 48-V automotive systems. The transition to electric-drive vehicles has also increased investments in HEVs and PHEVs.
Reducing the wire harness
The first major attempt to reduce the wire harness was the introduction of the zone architecture, which optimizes wiring in the vehicle by grouping power distribution, communication and load actuation based on location rather than by function, as shown in Figure 1. A zone architecture reduces vehicle wiring by using smart semiconductor fuses to replace the traditional melting fuses for power distribution and acting as a communication gateway from the central computer to sensors, actuators and electronic control units (ECUs).
Including a 48-V low-voltage rail in next-generation zone architectures could further reduce wire harness weight and costs. A 48-V rail enables reduced wire gauges while decreasing power losses in the wire harness and possibly shrinking printed-circuit-board (PCB) size given the reduction in current to deliver the same amount of power (25% compared with 100% at 12 V, for example). Figure 2 shows the benefits of moving from 12 V to 48 V.
In Figure 2, a zone control module needs 100 A to deliver 1,200 W at 12 V. In contrast, a 48-V rail requires only 25 A to deliver 1,200 W. Quadrupling the voltage and lowering the current by one-fourth reduces wire harness cost and weight by 85%.
For a window motor, 20 A at 12 V becomes 5 A at 48 V, resulting in a 60% cost savings and a 52% wire weight savings. As the load-current requirements decrease, the wire harness benefits of moving to 48 V also decrease.
While the main benefit of moving to 48 V is to reduce the wire gauge, wire cost is not the only factor. Today, installing thick wire gauges such as 4 AWG into vehicles is labor-intensive. Reducing the wire gauge in a 48-V system enables the use of automated manufacturing processes for wire harness installation, significantly reducing costs.
48-V architectures
When optimizing wiring harnesses for 48-V systems, OEMs will need to evaluate different architectures. Figure 3 shows three options when implementing a 48-V low-voltage rail: 48-V primary distribution and 12-V local; 48-V distribution and 12-V distribution; and 12-V distribution and 48-V high-current loads only.
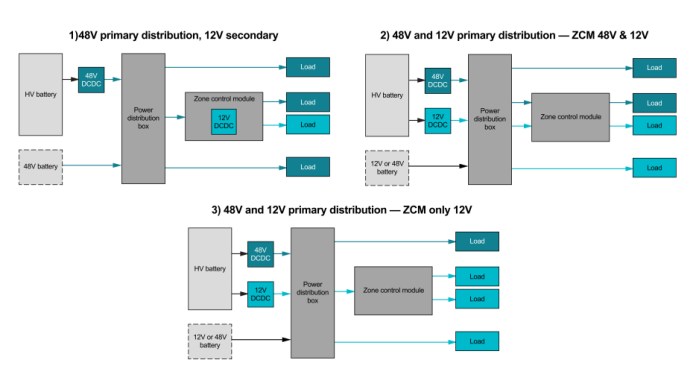
Figure 3: 48-V architectures—1) 48-V primary distribution, 12-V local; 2) 48-V and 12-V distribution—ZCM 48 V and 12 V; and 3) 12-V primary distribution, 48-V high-current loads (Source: Texas Instruments Inc.)
The least disruptive approach to 48-V design is to use the 48-V rail to power high-current loads and keep everything else at 12 V. However, 48 V and 12 V can be distributed to zone control modules or other ECUs, but this approach poses some challenges. The distribution of two voltages makes the routing of the wire harness a factor because routing both 12 V and 48 V in the same wire harness could result in a potential short from 12 V to 48 V. Functional safety considerations will also add costs, as there may be a need for redundant 12-V and 48-V supplies.
A more drastic design change is to move directly to a 48-V power distribution architecture and create a 12-V rail locally as needed. Implementing 48-V distribution with local 12 V is the best architecture to achieve the full benefit of moving to 48 V because it provides the greatest reduction in wire harness size and cost.
In a 48-V distribution with 12-V local architecture, there are many options to create a local 12-V rail at the ECU or select a different voltage entirely (25 V, 16 V, 5 V, 3.3 V). Figure 4 provides two possible power architectures: distributed and central 12 V for 48-V systems.
In a distributed architecture, multiple DC/DC converters with lower-power requirements can create a 12-V rail for different load groupings. This approach enables the use of DC/DC converters with integrated MOSFETs, along with the freedom to choose the voltage (such as 48 V to 3.3 V) and better thermal spreading across the PCB.
If OEMs want to reuse existing 12-V designs, a central 12-V rail is the easier approach. In this architecture, an always-on DC/DC converter provides power to functional-safety-critical loads, while a DC/DC converter with high-power requirements supplies the rest of the 12-V system. Another option is to use bidirectional 48-V to 12-V DC/DC converters to allow back-electromotive force from the motors, or positive transient voltage energy from the 12-V rail to flow back into the 48-V rail.
Design challenges
The design challenges when adopting a 48-V low-voltage rail include transient voltages, creepage and clearance requirements, electromagnetic compatibility (EMC) standards and IC costs.
Transient voltages are the main topic of conversation in 48-V systems. Today, 12-V systems are well-known, with standards such as ISO 16750-2 specifying voltage transient curves for worst-case events, such as load dumps. For 48-V systems, the standards available today (ISO 21780 and Liefervorschriften [LV] 148) were written for MHEVs requiring overvoltage points up to 70 V. But when factoring for switching transients or component margin, it results in component ratings much greater than 70 V.
The standards for MHEVs, while useful as a starting point, are not necessarily valid for an electric or hybrid system generating 48 V off the high-voltage battery without a high-power starter-generator system. The exact standards around a BEV 48-V low-voltage net are still being defined, but OEMs may begin developing their own standards to contain line transients below 70 V. Figure 5 compares a potential BEV standard against the existing ISO 21780 standard.
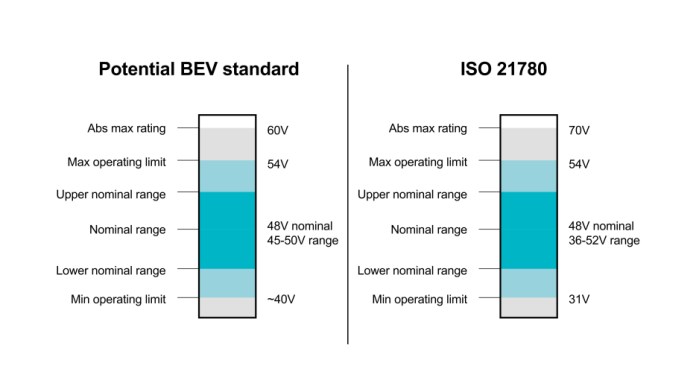
Figure 5: Potential BEV standard and ISO 21780 transient voltage comparison (Source: Texas Instruments Inc.)
While the difference between 60 V and 70 V may seem small, the cost of ICs to accommodate higher voltages doesn’t necessarily scale linearly. Also, even if it were possible to contain the supply ranges, it’s important to consider the potential for harness failure-mode events, which current standards such as ISO 7637-2 address.
Creepage and clearance requirements are industry-standard measurements of the shortest distance between all conductive parts on the PCB. They are critical design parameters for preventing arcing, which occurs when the voltage between two points exceeds the breakdown voltage. There are many standards for creepage and clearance (IEC 60664-1 and IPC 2221A), and OEMs may even have their own internal guidance. Moving from 12 V to 48 V increases creepage and clearance requirements, directly impacting IC packages, PCB layout, wire harness connectors and more.
A subtler impact of 48-V systems is that, while they help reduce conduction losses, switching losses also increase. This becomes relevant in EMC testing for switching power converters such as DC/DC converters and motor drives. Increasing the voltage (VDS) from 12 V to 48 V allows the current (IDS) to reduce. However, if the slew rate (tR + tF) in 48-V systems remains the same as 12-V systems, then the power-switching losses (PSW) quadruple.
While there are more factors that impact switching losses, Figure 6 illustrates how the slew rate impacts switching losses in 48-V systems. There are several methods to help reduce conducted emissions in DC/DC converters.
While 48-V systems can reduce the weight and gauge of the wire harness, saving cost in the actual copper of the wire and manufacturing, the conversation comes back to cost. The adoption of 48 V has many benefits and challenges that will affect cost in some way, whether at the IC level or system level. OEMs will need to decide when and how to incorporate 48-V systems to maximize benefits and reduce costs. The market and semiconductor suppliers are ready for 48-V systems, as evidenced by recent vehicle innovations.
Madison Eaker is a systems engineer on TI’s Automotive Body Electronics and Lighting Systems team, responsible for zone control modules and power distribution boxes. She has experience in EMI/EMC compliance, 48-V low-voltage architectures and automotive Ethernet in-vehicle network evolution.
Advertisement
Learn more about Texas Instruments