Imagine all of the cables and wire harnessing that are needed in a vehicle to connect a growing array of cameras, radars, sensors and sensor modules, displays, and electronic control units (ECUs). That’s a huge in-vehicle connectivity problem. In fact, a typical wiring harness assembly weighs about 60 kilograms (about 132 pounds), making it the third-heaviest part of the vehicle after the engine and chassis.
As more cameras, sensors, radars, displays, and other electronics get packed into a vehicle to implement new safety and infotainment features, automotive OEMs are looking for safer and more resilient high-speed in-vehicle connectivity.
But it’s not that easy. It comes with several big challenges, including limited bandwidth, too many cables (and the need to use heavier shielded wiring to meet electromagnetic compatibility [EMC] challenges), wiring length limitations, and harsh environments. And different use cases, such as infotainment, computing, and autonomous vehicles, need different connectivity technologies. The good news is that the MIPI Alliance’s recently released MIPI A-PHY standard will help solve these challenges.

Symmetric and asymmetric automotive data flows in various automotive systems (Image: MIPI Alliance white paper) Click for larger image.
As more devices get packed into a vehicle to deliver more safety features and support for autonomous driving, it will require multi-gigabit bandwidth, long-distance connectivity, and safe and resilient data links, said Daniel Shwartzberg, director of technical pre-sales at Valens, during his presentation at AutoSens 2020.
There are four key roadblocks that automotive OEMs face today for wired in-vehicle connectivity, and the first is limited bandwidth, he said. “Solutions today are running into the bandwidth wall — not only in terms of the amount of data that they can transfer but also the fact that it needs to be extremely time-sensitive when we’re thinking about sensors for advanced driver-assistance systems [ADAS] or autonomous applications.”
This also means that latency needs to be low because a delay on a signal can be critical for safety applications, he added.
The second challenge centers around the wiring harness itself. “There [are] just too many wires, too many cables going into the vehicle today,” said Shwartzberg. “We’re trying to connect an ever-increasing number of ECUs from various points around the vehicle, and this is becoming extremely difficult to achieve.”
This plays right into the third challenge of wiring lengths. “There are distance limitations with the existing solutions today in terms of how far we can run a signal through the vehicle, and that has a direct impact on physical topology — the physical layout of the sensors of the ECUs within the car,” said Shwartzberg.
The fourth challenge is the harsh automotive environment, including electromagnetic interference (EMI), EMC, and temperature. It’s not just the extremely harsh automotive electromagnetic environment, Shwartzberg said. “It’s also the fact that the vehicle has very severe temperature swings and the cables are exposed to aging and to rough handling during manufacturing. And throughout the lifetime of the vehicle, cables are exposed to vibrations, heat cycling, etc.”
What does it take to make cars see better? It’s complicated. Multiple sensing modalities, faster processing power in the vehicle brain, new car architecture with updated in-vehicle network, self-cleaning sensors, common sense layer and a lot more.
Multi-gigabit communication
These challenges contribute to additional roadblocks for automotive OEMs. One of those is the need for high-bandwidth links of at least 1 Gbits/s up to 10 Gbits/s (and in the future, beyond those speeds), as well as the need for very resilient communication links.
Emerging ADAS/AV trends are driving the need for multi-sensor fusion that requires central “brains” connected using long, high-throughput links to multiple sensors at the edge of the vehicle, explained Shwartzberg. However, the harsh in-vehicle environment poses challenges to these safety-critical data links, requiring shielded cables to tolerate the high EMI levels.
In addition, an exponential increase in ADAS/AV data rates is pushing conventional automotive communication technologies to their boundaries and even beyond in terms of required immunity margins at these rates and component-level EMC testing methods to guarantee safe vehicle lifespan operation over shielded cables, according to Shwartzberg.
As the bandwidth goes up, this introduces a lot of EMI challenges, he said. “As the data rate goes up, the signal-to-noise ratio tends to go down, and suddenly, electromagnetic noises can have a marked effect.”
Of course, automotive OEMs and Tier One suppliers test for EMC, but Shwartzberg said the current EMC specifications are lagging behind as technologies move to much higher bandwidths, and there is a “desperate need for safe, robust, resilient links.”
Shwartzberg said that some of the EMC and EMI risks like crosstalk between cables and unpredictable electromagnetic environments are already being managed, but it’s the new, emerging EMC concerns that the industry doesn’t have any experience with that are causing some issues. Those cited include multi-gigabit bandwidth, more mission-critical systems (ADAS/AV), a lack of field experience with links at or higher than 1 Gbits/s, EMI noise, insufficient EMC testing specs, cable flexing/aging and shield deterioration, and electric vehicles with very high current flows that generate very high electromagnetic noise.
These factors can lead to system failures in the field, increased warranty costs, vehicle recalls, and a risk of injury or death.
One of the trends in the automotive industry is a move to “zonal architecture” to solve some of these challenges. This type of architecture offers several benefits: high-speed data transmission, higher bandwidth, weight reduction, and less complexity.
Shwartzberg noted Aptiv’s new smart vehicle architecture (SVA) as an example. It’s a modular zonal architecture that is designed to simplify manufacturing and vehicle assemblies.
At the center of the SVA architecture (see image below) is the central compute cluster with power data centers, or zonal hubs, at the corners of the vehicle, where the multiple sensors feed into each hub and the data is then fed into the central compute cluster.
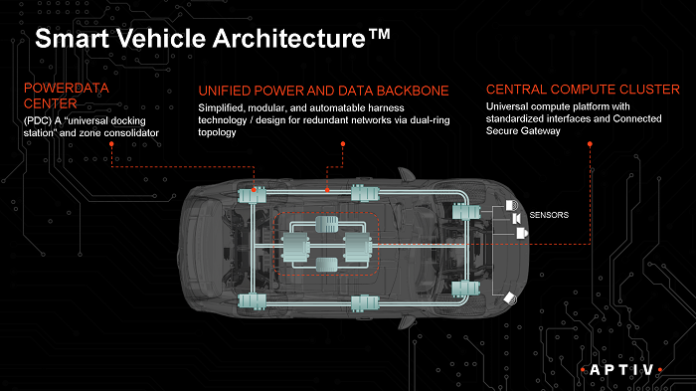
(Source: Aptiv)
“These sorts of topologies are needed in order to reduce the number of ECUs in the vehicle, but the amount of bandwidth needed on each link suddenly goes up dramatically as well,” said Shwartzberg. “I have fewer ECUs, but I still have the same amount of data and they’re going over less wiring, so I need faster links, higher-bandwidth links, and again, this is all safety-critical, so those links need to be extremely robust and secure.”
MIPI A-PHY
To meet these emerging challenges, Valens offers ultra-high-speed in-vehicle connectivity solutions — physical layer technologies — that simplify vehicle architectures. They are also designed to be scalable and future-proofed and support symmetric (HDBaseT) and asymmetric (MIPI A-PHY) applications.
Valens Automotive’s PHY technology was selected by the MIPI Alliance as the baseline for the new MIPI A-PHY physical layer standard, released to alliance members in September 2020. Targeting automotive applications, the MIPI A-PHY v1.0 is the first industry-standard, long-reach serializer-deserializer (SerDes) physical layer interface. The new specification provides an asymmetric data link in a point-to-point topology, providing high-speed unidirectional data, embedded bidirectional control data, and optional power delivery over a single cable.
It targets high-speed links for cameras, displays, and sensors through native CSI-2 and DSI/DSI-2 interfaces, which supports autonomous driving and other use cases. According to the MIPI Alliance, the new A-PHY v1.0 standard provides:
- High reliability: Ultra-low packet error rate (PER) of 10–19 for unprecedented performance over the vehicle lifetime
- High resiliency: Ultra-high immunity to EMC effects in demanding automotive conditions
- Long reach: Up to 15 meters
- High performance: Data rate as high as 16 Gbits/s with a roadmap to 48 Gbits/s and beyond; v1.1, already in development, will provide a doubling of the high-speed data rate to 32 Gbits/s and increase the uplink data rate to 200 Mbits/s
Why is the MIPI A-PHY such a big deal? “At the technical level, it is a standard which is extremely resilient,” said Shwartzberg. “It has mechanisms built in to handle cable aging and deterioration, and we’re talking about cable reaches of up to 15 meters, while still passing all of the most stringent EMC requirements from OEMs and Tier One suppliers. With a view to the future, it’s a standard that scales up in terms of the bandwidth.”
One of the key benefits is that it helps reduce signal loss in the cable. “As the frequency increases and as bandwidth increases, signal loss increases — that’s the physics of the cable, unfortunately,” Shwartzberg said. “If we run with an NRZ signal, we lose about –60 dB when talking about a 16-Gbits/s link. But Valens’s and now MIPI A-PHY solutions use pulse-amplitude modulation [PAM], which is multi-level signaling that allows for the same 16 Gbits/s, depending upon whether we’re using four levels of PAM [PAM-4] signaling or 16 [PAM-16] to greatly reduce the symbol rate and thus greatly reduce the amount of signal loss in the cable.
“So we operate at a much better operating point on the cable to reduce the losses,” he added. “In addition, we have built-in mechanisms for just-in-time noise cancellation and physical-layer ultra-fast retransmission mechanisms for error correction that guarantee all data packets are actually successfully passed across the link.”
There are several use cases where this type of technology comes into play, including multiple sensors feeding into a single ECU or more than one SoC for redundancy or increased processing power. It also offers increased scalability in terms of the number of sensor modules that can be connected to the same ECU. It also can be used for ECU-to-ECU connectivity.
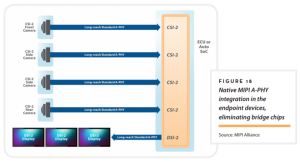
Fig. 18 in MIPI Alliance’s white paper illustrates the simplest direct connection between an A-PHY-equipped image sensor and an A-PHY equipped ECU or automotive chip. (Image: MIPI Alliance) Click for larger image.
Valens’s A-PHY chipsets allow for the convergence of multiple different data types onto a single-wire pair, and depending on the chip family, it can even run on unshielded twisted-pair (UTP) cable.
“We can still pass EMC tests even when running over the unshielded pair,” said Shwartzberg. “This is a multi-gigabit link and it is bidirectional, so we run data simultaneously over the same pair at the same time. For our own HDBaseT protocol, this is a symmetrical link, so the same bandwidth is running in both directions, and for MIPI A-PHY, it’s an asymmetrical link.”
A hard-wired DSP built into the silicon provides active noise cancellation, adaptive equalization, and echo cancellation to ensure mission-critical links.
“With MIPI A-PHY, it brings a standard solution to the automotive industry, and we already see emerging a large ecosystem of interoperable devices from different vendors,” said Shwartzberg.
A new book, AspenCore Guide to Sensors in Automotive: Making Cars See and Think Ahead, with contributions from leading thinkers in the safety and automotive industries, heralds the industry’s progress and identifies the engineering community’s remaining challenges.
It’s available now at the EE Times bookstore.
Advertisement
Learn more about Valens