The countdown has begun: Autonomous, electrically powered, connected cars will revolutionize the whole automotive industry in the next few years — a change that goes far beyond web access or the disappearance of the steering wheel and pedals. Self-driving connected cars will take us into a new transport era that is more efficient, economical, clean, and ecological, and lithium-ion (Li-ion) batteries and battery management systems will be key to that electric mobility (e-mobility).
According to experts, these systems will transform the way we travel in the years to come, redesigning the future of mobility, smart cities, and interactive communities. The growing focus on connected vehicles, perhaps with high-speed 5G networks, has been accelerated by the fact that they will be largely electric.
The new component requirements needed in the evolution toward electric, connected, and self-driven vehicles will center around traction (electric engine, batteries, and transmission components), advanced driver-assistance systems, autonomous functions (adaptive suspension, active steering and braking systems, vision sensors), the application of new materials, and passenger compartment design (including increased interior insulation as well as gesture recognition and augmented-reality displays).
However, the battery is the beating heart of any electric vehicle (EV). In order for the connected car to prove it is intelligent, it must optimize its power consumption by monitoring and controlling the battery charge.
The main concern lies in power drain, which is the process by which lithium batteries gradually dissipate energy caused by latent absorption related to electrical systems that remain active even when the vehicle is switched off: safety systems, on-board computer systems, and telematics. Energy loss can be as much as 1% to 2% per day. Therefore, it is necessary to periodically check that the charge status of the main battery pack is optimal.
The efficiency of a Li-ion battery in terms of how much energy it can deliver in relation to its size and weight has improved considerably over the years. However, researchers still face challenges to improve power density, durability, cost, charging time, and safety. Monitoring electrical performance is key to the success of Li-ion battery applications.
The challenge for automotive electronic system designers is to implement a battery management system (BMS) that ensures safe operation, long battery life, and the separation of low- and high-voltage domains without requiring complex circuits with a high number of components.
Batteries for e-mobility
Li-ion batteries are a key technology for future forms of mobility and energy conservation and are gaining ground thanks to features such as higher power density and lower cost. Mass production of these batteries for e-mobility is increasing significantly, mainly due to the trend toward EVs. According to several research analysts, approximately 64% of these batteries were produced for e-mobility worldwide in 2018, and by 2025, this will rise to well over 85%.
This growth is also due to the fact that they are becoming increasingly economical. According to the latest forecasts presented at several e-mobility forums, by 2021, the price of Li-ion battery systems will have fallen to such an extent that electrically powered vehicles will be competitive with their combustion engine counterparts.
The main challenges required to deliver high performance are increased range, high recharging speed, and reduced maintenance costs. Many companies offer electric storage solutions that provide a wide operating temperature range and extend the range of hybrid (HEV), plug-in hybrid, and fully electric vehicles. Advanced Li-ion battery technology is designed to improve energy density.
There are two major design issues with Li-ion battery cells: One is material chemistry, the other is electronic, which means that when overcharged, it can cause permanent damage and overheating. Therefore, it is important to have a BMS to provide protection and energy control. The monitoring system is essentially the “brain” of a battery system; it measures and reports information, which is crucial for the system and protects it from damage in a wide range of operating conditions.
Battery management systems
Battery systems for EVs and HEVs must be designed to support long inactivity periods. For this reason, the standby power supply of the module circuit must consume much less energy than self-discharging the battery cells, which significantly reduces the risk of overcharging. To track the load dynamics of the EVs/HEVs, including the discharge and charging mode of operation, the electronic battery monitoring components check the cell voltages at a rate of 50 samples per second or more. This implies a high rate of raw data flow from the battery pack, sometimes with a 60-kbits/s payload for a 96-cell pack.
The arrangement of battery cells needs special attention, as their size and weight have practical implications for maintenance and distribution within the vehicle. Batteries organized in modules help distribute the weight and offer ease of management.
In practice, the main functions of a BMS for EVs can be summarized as follows:
- Battery protection to prevent operations outside its safe operating area
- Battery monitoring by estimating the state of charge (SOC) and state of health (SOH) during charging and discharging operations
- Optimization of the battery by balancing the cells to improve battery life and capacity, thus optimizing the driving range for e-mobility vehicles
IC solutions
The BMS makes it possible to monitor battery usage and thus optimize overall vehicle performance. This system further manages the rechargeable battery by controlling the operating area, balancing the SOC, and protecting it.
The global market for automotive battery management systems is segmented by battery type, vehicle type, connectivity topology, and region, according to Allied Market Research. There are a variety of players in this market with a range of offerings. Here are a few examples.
Infineon Technologies AG offers its TLE9012AQU multi-channel battery monitoring and balancing system IC for Li-ion battery packs used in automotive, industrial, and consumer applications. The TLE9012AQU provides four main functions: cell voltage measurement, temperature measurement, cell balancing, and isolated communication to the main battery controller. Additionally, the TLE9012AQU provides the necessary diagnosis tools to ensure proper function of the controlled battery (Fig. 1).
Analog Devices Inc.’s (ADI’s) BMS based on the AD7284 management board monitors eight-channel Li-ion batteries and includes all the functions necessary for monitoring stacked batteries and diagnostic features that include detection of open inputs, communication, and power supply failures (Fig. 2). The AD7284 monitoring system is well-suited for monitoring the Li-ion battery in EVs/HEVs and stationary power applications.
The AD7284 is characterized by a multiplexed cell voltage and auxiliary analog-to-digital converter (ADC) measurement channels to support four to eight battery management cells, an internal temperature sensor, and a control timer. The four auxiliary ADC input channels are used for temperature measurement and system diagnostics.
The complete monitoring system with 14-bit resolution integrates multiple voltage input channels and an auxiliary ADC. The components on the motherboard include power and interfaces isolated using the ADuM1201 and ADuM5401 digital isolators and the power supply through the ADP3303 and ADP7104 regulators.
Renesas Electronics Corp. offers the ISL78692 and ISL78693 automotive-grade single-cell battery chargers that extend the life of Li-ion, lithium polymer (Li-polymer), and lithium iron phosphate (LiFePO4) batteries used in automotive emergency call (eCall) systems.
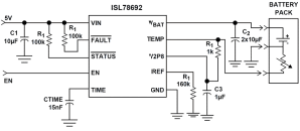
Fig. 3: A block diagram of the ISL78692 from Renesas Electronics (Source: Renesas Electronics Corp.) Click for a larger image.
The ISL78692 is an integrated single-cell Li-ion or Li-polymer battery charger capable of operating with an input voltage as low as 2.65 V (cold crank case). It operates as a linear charger when the AC adapter is a voltage source and can also work with a current-limited adapter to minimize the thermal dissipation. The ISL78692 features charge current thermal foldback to guarantee safe operation when the thermal dissipation of the printed circuit board is limited due to space constraints (Fig. 3).
Battery monitors capture key battery parameters such as voltage, current, and temperature and relay this information to a microcontroller. These devices form a part of a complete monitoring and balancing solution for next-generation high-power systems such as EVs, power tools, energy storage systems, and e-mobility applications.
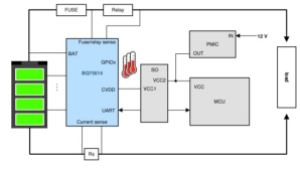
Fig. 4: A simplified system diagram of TI’s BQ75614-Q1 (Source: Texas Instruments) Click for a larger image.
The BQ75614-Q1 device from Texas Instruments Inc. provides cell voltage measurements up to 16S battery modules in less than 200 µs. The integrated front-end filters enable the system to implement with simple, low-voltage-rating, differential RC filters on the cell input channels. It also comes with an integrated current measurement with the option to synchronize with cell voltage measurements for better SOC calculation. The device supports autonomous internal cell balancing with temperature monitoring to auto-pause and resume balancing to avoid an overtemperature condition (Fig. 4).
STMicroelectronics’ automotive offering for BMS includes highly integrated chips that can provide the highest accuracy measurements for cell monitoring. The L9963 is a Li-ion battery monitoring and protection chip that monitors up to 14 stacked battery cells to meet the requirements of 48-V and higher-voltage systems.
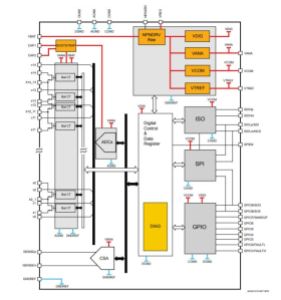
Fig. 5: A block diagram of STMicroelectronics’ L9963 (Source: STMicroelectronics) Click for a larger image.
Each cell voltage is measured with high accuracy, as well as the current for the on-chip coulomb counting. The device can monitor up to seven NTCs. The information is transmitted either through SPI communication or an isolated interface (Fig. 5).
Conclusion
The growth in the EV market will bring new solutions to optimize energy management. In particular, the battery will play a big role with battery management systems, helping to optimize the performance of the electric car while ensuring the safety of the battery pack.
A new book, AspenCore Guide to Sensors in Automotive: Making Cars See and Think Ahead, with contributions from leading thinkers in the safety and automotive industries, heralds the industry’s progress and identifies the engineering community’s remaining challenges.
It’s available now at the EE Times bookstore.
Advertisement
Learn more about Analog DevicesInc.Infineon TechnologiesRenesas Electronics AmericaSTMicroelectronicsTexas Instruments