By connecting machinery and tools, the industrial internet of things (IIoT) allows manufacturing companies to improve the visibility of production in real time. The huge amount of data collected by IIoT devices allows you to optimize production, improve the quality of products and services, apply predictive maintenance, automate the supply chain, and more. The link between IIoT and Industry 4.0 is very close, considering that IIoT infrastructure is what allows an industrial reality to become fully digital and smart. Despite the difficult economic climate of the past two years, investments in IIoT have marked a positive trend, with further growth forecasts for the next few years.
Energy efficiency is taking on a fundamental role in the industrial world. The goal of the “Green Factory” is now being pursued not only to meet the needs of the environment and sustainability but to increase the profitability of the industry. The rising cost of energy and its impact on the environment have made energy efficiency one of the primary objectives of Industry 4.0.
Power management and energy efficiency
Power management systems have the task of monitoring in real time the energy sources required for carrying out industrial activities, providing useful information related to power distribution parameters and identifying patterns and trends. The main objective of power management is to ensure the supply of energy, particularly its availability, reliability, and quality.
Energy efficiency, on the other hand, is more focused on aspects related to cost reduction that a company can achieve by reducing energy losses and reducing environmental impact. Industry 4.0, which has now entered all major industrial sectors, cannot ignore energy efficiency. The bond is so close that today, we speak more properly of Energy 4.0, a context in which smart grids allow the management of different energy sources (including renewable energy) and their distribution. On the other hand, the integration of different energy-generation sources in an increasingly distributed market requires management techniques capable of guaranteeing quality, sustainability, and efficiency in energy consumption — objectives that, once again, digitization can help achieve.
Benefits of IIoT for smart factory
IIoT substantially contributes to the conversion of the industry into a smart-factory reality, bringing benefits such as:
- Higher efficiency: Sensors continuously monitor the system and collect useful data to determine the correct functioning of the machinery, the progress of processes, and energy consumption. This allows for a better understanding of how resources are employed and whether a more effective way to use them can be found.
- Increased safety: Some production activities, such as assembly, molding of parts, inspection, and control of machinery, can pose serious risks to the health of operators. The ability to remotely manage the acquisition of data and to entrust the most dangerous activities to robots and intelligent machinery allows the company to guarantee better protection of the safety of workers and maintainers.
- Downtime reduction: Predictive maintenance allows you to estimate the time left before a failure occurs. By planning the appropriate interventions in advance, it will be possible to reduce the risk of unplanned downtime and the associated costs, guaranteeing greater resilience to the business.
- Balance between energy supply and demand: Compliance with the ISO 50001 standard allows industries to equip themselves with an energy management system to continuously improve energy efficiency. With an ISO 50001 certification, companies are able to gain knowledge of internal energy consumption and can monitor and reduce their energy needs.
Energy efficiency trends
We have seen how energy efficiency has become a primary goal in IIoT applications and how this can contribute to the full realization of the plans envisaged by Industry 4.0. The main trends in energy efficiency will now be examined, focusing on the technical content and the benefits provided.
Sensors
Because sensors are the basic element of any IIoT application, it is important that they themselves are very energy-efficient. Several hundred or thousands of sensors can be used in a single IIoT application, so an efficiency improvement of a few percentage points has considerable weight. Furthermore, because most of these sensors are battery-powered, it is essential to try to extend their autonomy as much as possible. Figure 1 shows the block diagram of an electricity meter, taken from a reference design by NXP Semiconductors. The choice of all the required components (MCU, communication transceiver, display, etc.) must give priority to low-consumption components capable of supporting low-power operating modes with very low quiescent current. It follows that energy-efficiency improvements in sensors can be obtained through an appropriate and accurate design of the IoT device.

Figure 1: Electricity meter block diagram. Click for a larger image. (Source: NXP Semiconductors)
Edge computing
One of the main dilemmas of any IIoT application is finding the right compromise between processing performed on the cloud and local processing. The first has the advantage of requiring low computing power but needs higher bandwidth and longer transmission times, with a consequent increase in current consumption. However, the availability of high-performance microcontrollers, combined with the ability to run artificial-intelligence algorithms in real time, such as deep learning, is driving the transition of many applications toward edge computing.
Smart-grid integration
Without the need for human intervention, the smart grid monitors local variations in power demand and reacts automatically. It requires grid-to-consumer communication in both directions, in real time, allowing consumers to adapt their energy consumption depending on personal preferences such as pricing and/or environmental concerns. Communicating with cellular towers or other similar infrastructures, the smart grid sends crucial statistics like immediate power use, cumulative power consumption, maximum demand, and more.
Digital twins
The term “digital twin” refers to the virtual replica of a physical resource, represented by an object, process, system, or device. Digital twins are used for various purposes, particularly to optimize production and for predictive maintenance. Compared with the Industry 4.0 paradigm, therefore, this type of approach is state-of-the-art.
Mixed-reality devices allow you to create a virtual replica of industrial machinery, view them, and place them exactly in the destination location, evaluating the correct dimensions and anticipating any problems in the installation phase. Through digital twins, it is also possible to conduct simulations and stress tests without having to stop production.
Energy harvesting
The number of devices connected to the IIoT is growing all the time. Machine learning in the cloud, energy-harvesting technologies, and ultra-low–power radio transmission combine to create a flexible infrastructure for monitoring industrial plants, equipment, and buildings that do not require hardwired power or communication connections.
Small and simple sensors can exploit energy harvesting to extract energy from the environment and convert it into a ready-to-use power supply. These sensors do not require batteries for their operation, as they are powered by the environment’s heat, light, or motion. Temperature, humidity, and motion sensors, as well as actuators, can today be installed almost anywhere. Sensors can communicate with each other and with a controller, or gateway, which can be connected to the cloud, enabling the smart-factory concept.
Efficiency in power conversion
In industrial plants, there are many devices that use a power supply or a power-conversion system. For several years, the trend has been to almost exclusively use switching power supplies, capable of offering high efficiency values, at the expense of a non-negligible RF emission. In some applications, linear converters (less efficient but with practically zero electromagnetic emissions), are still preferable. In AC/DC converters, it is necessary to introduce a power-factor–correction stage to improve the quality of the signal and therefore the efficiency of the conversion. Further efficiency improvements are now obtainable with the introduction of wide-bandgap semiconductors, such as silicon carbide (SiC) and gallium nitride (GaN). Thanks to their superior physical properties, SiC and GaN devices can replace traditional silicon-based components (MOSFETs and IGBTs) with the advantage of higher energy efficiency, higher working voltages, higher maximum temperatures, and better heat dissipation, as well as lower weight and size.
Smart robots
In industry, robots are used to carry out repetitive jobs previously performed by humans. In this area, one of the most recent and fascinating innovations is computer vision, particularly stereoscopic vision. Stereoscopic cameras, emulating the typical visual abilities of the human being, allow the robot to perceive not only the surrounding environment but also the depth, or distance, of the various points of the image. This allows for greater accuracy of movement and precision in grasping and releasing various types of objects.
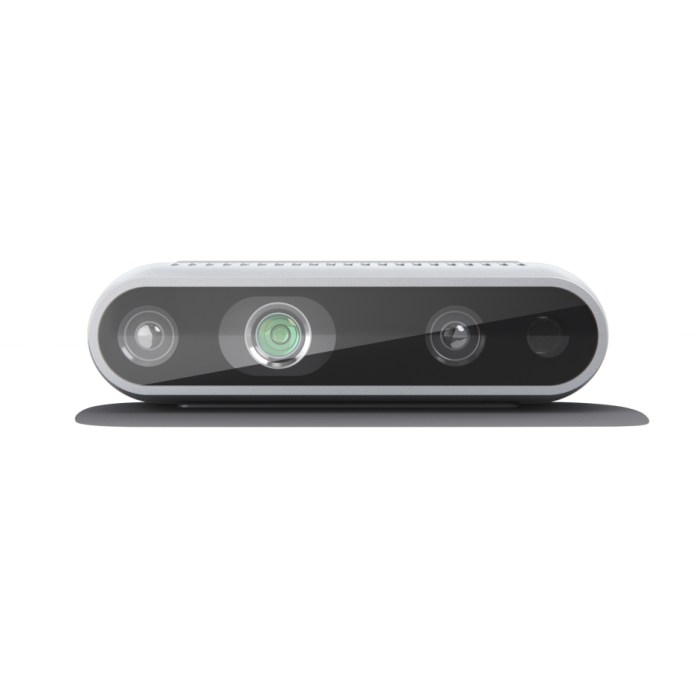
Figure 2: The Intel RealSense D435i depth camera enables the creation of challenging applications in industrial robotics. Click for a larger image.(Source: Intel Corp.)
Conclusion
The industrial sector is responsible for consuming a high percentage of the energy used worldwide and consequently is also one of the largest contributors to greenhouse gas emissions. A greater responsibility for the environment is stimulating the search for new solutions capable of reducing energy consumption and making production more efficient and respectful of the environment. IIoT and Industry 4.0 offer several opportunities to support these efforts. The integral use of technology, together with optimized production processes through intelligent and efficient methods and applications, can help improve production processes and reduce energy consumption.
Advertisement
Learn more about Intel Corp.NXP Semiconductors