Wireless battery management systems (wBMSes) are breaking down the barriers to widespread adoption of electric vehicles by delivering increased safety and reliability while improving drive range and lowering cost. Wireless BMS solutions also deliver greater flexibility in battery placement and scalability across EV platforms. In addition, advanced monitoring capabilities give batteries a second life.
Whether wired or wireless, the primary job of the BMS is to protect the batteries, preventing operation outside of its safe operating area. It also monitors the batteries for state of charge (SOC) and state of health (SOH) during charging and discharging and performs cell balancing for battery optimization, improving battery life and thus extending EV range.
The BMS monitors several battery cell parameters like overvoltage/undervoltage as well as overcurrent/undercurrent to ensure that the cells are not being overstressed. It also monitors temperature to safeguard the cells from overheating or swelling.
The battery management system will take the data from all of the batteries in series and make sure it is operating within safe limits, and once the safety is established, the next key role is to optimize the performance of the battery, said Shane O’Mahony, wBMS marketing manager at Analog Devices Inc.
The biggest task of the BMS is to keep the battery safe, agreed Tony Allen, BMS applications manager for the Automotive Analog Power & Video Business Division, Automotive Solution Business Unit, at Renesas Electronics Corp. “In terms of how it does that—with voltage readings, current readings, temperature readings and impedance measurements—you are gathering all this raw data from the cells using the BMS front end. All of that [data] goes to the microcontroller [MCU], and the MCU uses that data in real time to calculate SOC, which is essentially the remaining range, and SOH, which is the state of the overall battery.”
Today, most EVs use a wired BMS to monitor the SOH and SOC of the battery cells or packs, and these systems are considered to be safe and very robust. However, wired BMS solutions require complex wiring, connectors, isolation devices and other components, which add to the weight and cost of the EVs. The wiring harnesses and connectors are also common sources of failures, adding to maintenance and repair costs. There are also potential challenges with manual labor (routing of the cables) and latency issues around data collection.
By removing the wire harness, the wBMS enables faster battery pack manufacturing and assembly as well as automation to streamline and scale EV fleet production, according to ADI.
As a result, many automakers are looking at wBMS solutions that deliver lower weight by eliminating the wiring, connectors and other components required in a wired BMS, increasing the driving range, which is still a big concern for consumers. It also improves reliability by eliminating the wiring harnesses and associated components—often sources of failure—and reducing manufacturing cost with easier maintenance and replacement of the battery module. It also allows for greater flexibility in terms of where the battery modules are placed.
Once the weight of the battery system is reduced, the mileage increases, and this is very important for use-case applications, said Yin Yang, senior marketing manager for Wireless Charging & BLE, Automotive Analog Power & Video Business Division, Automotive Solution Business Unit, at Renesas Electronics Corp. “Not only is the cost down and the car is lighter, but with the same battery, you can travel farther, so those are the benefits of wireless.”
“Every ounce of weight in the vehicle is important … the weight savings is really a massive benefit, and that ultimately extends your range,” said Niall Lyne, vice president of the Automotive Analog Power & Video Business Division, Automotive Solution Business Unit, at Renesas Electronics Corp.
BMS solution suppliers also believe that by transitioning to wireless connectivity, it will make it easier for automakers to scale their EV platforms across different vehicle models. They agreed that major automotive OEMs are all looking at wireless systems.
Thanks to these advantages, power IC manufacturers like ADI, Renesas Electronics and Texas Instruments Inc. are developing new wireless solutions that will enable automotive OEMs to reduce design complexity and cost. These advanced BMS systems can monitor and manage individual battery cells and packs, contributing to higher battery efficiency and reliability.
It’s about the data
Parameters have to be measured as fast as possible, whether it’s a wireless or wired BMS, said Lyne. “When you do the calculation for the SOC, you want to be able to monitor the current and voltage and all the parameters instantaneously across the cells in the pack, and that’s very important,” he added.
But the data is processed differently in wired and wireless BMS solutions.
In both systems, there are battery sensors on the battery modules, and they monitor voltage, temperature and other diagnostics, said O’Mahony. He explained that in a wired system, the data travels over the wire. The raw data goes to the central processing unit, one per pack, which will process the data to determine if it is in a safe operating region, what the state of charge is, and what the state of health is and provide data for the charging and battery gauge algorithms.
“In a wireless system, it is a little bit different,” said O’Mahony. “We add a secure radio with processing to every battery section. If you had, for example, a 400-V battery like a typical car, there may be eight battery modules or eight battery sections, so each battery section now has its own wireless unit with secure processing and safe processing. The data is gathered and can be processed by the edge unit and then transported back wirelessly to a similar central controller.”
With this distributed processing system, it can collect the data faster because everything is at the edge, he added. “You can either decide to process like you always did in the wired system centrally or you can now start to do some edge processing with the wireless system.
“Both wired and wireless systems have to achieve the same level of basic functionality to keep batteries safe, but with the secure edge processor, you can sometimes get more out of the data, and it can also alleviate the load on the central processor,” said O’Mahony.
Another new capability thanks to the wBMS is that the battery modules can be monitored even before they are placed in the EV.
With the wireless BMS, because secure processing is added to every battery module as soon as the module is created, it can start measuring and processing data even before it’s in the car, sitting in the factory or being transported to the factory from the battery maker, said O’Mahony. “It provides life-cycle data from cradle to grave across the full life cycle.”
It is also the first time that security is at this level, said O’Mahony. In a wired system with a simple monitor on the battery, if the battery is swapped with a similar monitor, it doesn’t know the difference, whether it is a genuine or counterfeit battery, he added.
With the wireless BMS, each unit can authenticate itself, so when it is brought into the full pack, it will know if it is a genuine unit or if it is a counterfeit, so there are some new possibilities with the wireless system, O’Mahony said. The battery packs can automatically reject the bad battery modules, so they aren’t added to the pack.
By having data across the life cycle, from assembly to warehousing to transport, it makes it more likely to spot issues like a particular battery that is abnormal or manufactured incorrectly, which can avoid vehicle recalls, said O’Mahony.
Scalability and battery placement
One of the biggest benefits by using a wBMS is scalability. It enables an automotive OEM to easily use the same module design across different vehicle models and use cases.
They can use a common wBMS platform that is software-configurable over the air for each vehicle model. This is a key reason why GM adopted wBMS for its Ultium battery platform, enabling the company to scale across its brands and vehicle segments. The automaker attributes the wBMS to enabling the widespread electrification of its fleet.
GM selected ADI’s wBMS solution. “All you need to worry about is the different software, and that is the simplicity of it,” O’Mahony said.
Lotus Cars has also adopted ADI’s wBMS for its new line of EV production cars within the next five years. They plan to develop a new ultra-lightweight powertrain architecture and wBMS.
Automotive manufacturers use the battery packs like building blocks, explained Lyne.
They want to have the same battery pack design and drop them into each vehicle at different sizes (number of cells), and they want the architecture to be the same because a lot of development goes into that one system, he added.
“You can then do your EMI/EMC testing, which is very expensive—probably a few hundred thousand dollars for each vehicle—but if you have the one common battery pack system and architecture, you’re saving massive costs, development time and scheduling, and then you can populate the different pack sizes for different customers,” said Lyne. “It’s a lot easier with wireless because you don’t need to have the cable harnesses in place that restrict your maximum number of cells, which is the case today. Plus, the weight of it.”

Niall Lyne (second from left), vice president of Renesas Electronics’ Automotive Solution Business Unit, with colleagues (Source: Renesas Electronics Corp.)
However, there are still testing challenges.
Each of the different vehicle models from an automotive OEM has a different Faraday cage, and how your wireless device performs in that Faraday cage will differ from one vehicle to the next, said Lyne. “So even though they may have the one battery pack for the different vehicles, they may have other immunity issues within the vehicle because of size, frame and how it’s built.”
How do you address the challenges? That’s where the secret sauce comes in, said Lyne. In addition to performing the different EMI/EMC testing and how Bluetooth Low Energy (LE) behaves in the environment, it is also affected by factors like the board layout and RF antenna design.
Wireless BMS can also help with the placement of the modules in the vehicle. “You no longer have to think about where the connections are or how to connect the data,” O’Mahony said. “If an OEM is designing 10 different types of cars or applications, this is definitely going to help mechanically, because at the end of the day, you don’t have to connect the harnesses through manufacturing, so it will be easier, faster and more reliable to do it if you have fewer mechanical tasks to do.”
Wireless BMS challenges
There are other challenges, such as security and selecting the wireless protocol. There seems to be some debate over which is better—an industry-standard wireless communications protocol or a proprietary standard.
With wireless BMS, there is the weight savings and better reliability because you don’t have the physical connectors, which can fail over time and are affected by vibration, for example, said Allen, but you do need to be more concerned with security.
“So the wireless protocol has all this security built in that the wired system doesn’t need because it is hardwired,” Allen said. “You can’t penetrate it from outside. In terms of the data that is exchanged, it’s all the same.”
Renesas selected Bluetooth LE as the wireless protocol for its wBMS solution, thanks in part to its acquisition of Dialog Semiconductor. Bluetooth LE is a known technology, proven in the industry, and it’s an open standard, with many people worldwide working with the technology, and it has encryption built in, said Lyne.
With the encryption and other security features, the battery packs can’t be hacked, which also means that the batteries can’t be swapped out for counterfeits.
So why select Bluetooth over other wireless communication standards? It’s about the higher bandwidth.
“We want to monitor the batteries’ data in real time as fast as possible,” said Lyne. “BLE has the highest bandwidth, which means we can actually monitor the batteries’ data as fast as we can.
“Ultimately, OEMs want to measure equivalent impedance across the cells, and from that, they can determine the health of the cell and the range left in the cell,” he added.
“There is a proprietary standard [used for wireless BMS] that is not as fast as BLE, which cannot meet the timing criteria that’s required for a battery management system, and it has much higher power consumption than ours,” said Lyne. “Also, BLE is a much lower cost.”
Lyne said automotive OEMs prefer to use a standard, and second sources, especially due to the capacity constraints over the last two or three years. They will also be able to use BLE in other applications in their vehicle and piggyback off that, he said.
However, some BMS suppliers believe proprietary wireless standards tailored for the use case is the best option, allowing for better handling of issues like interference, security and safety.
ADI’s wireless BMS solution, as an example, uses its own proprietary network built from the ground up, along with the radio hardware.
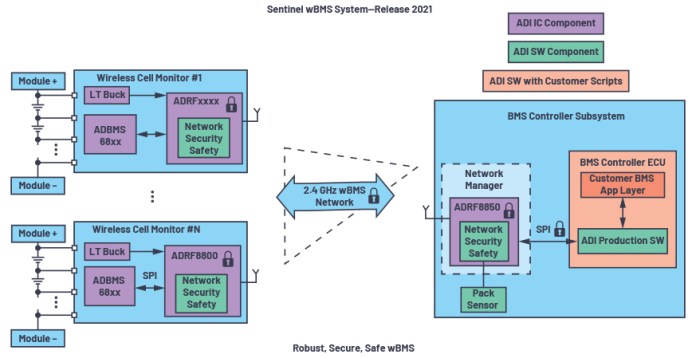
ADI’s Sentinel wBMS is a purpose-built automotive battery management system. (Source: Analog Devices Inc.)
“Wireless in an EV battery pack is challenging, and we saw early on that it would need a proprietary system that was tailored to that use case,” said O’Mahony. “One year after launch, ADI’s system is the only one in production.
“It’s not an easy problem to solve, but you do need to push customized application-specific networks and hardware to solve this problem,” he added.
Security also needed to be addressed with wireless, and again, ADI built the security from the ground up, O’Mahony said. “We also saw that there was a new ISO 21434 cybersecurity standard coming to automotive.”
ADI’s wBMS is certified to ISO/SAE 21434 for cybersecurity risk management and is the first to meet this qualification, according to TÜV NORD Mobilität.
“The electric battery pack will definitely be one of the key critical systems to keep secure,” said O’Mahony.
Another reason ADI decided on a proprietary network and custom hardware was to handle interference, including in-band interference. O’Mahony said ADI needed a system that would operate correctly even in environments with strong interference, including in-cabin and outside the vehicle.
Safety was another big issue for automotive OEMs, which ADI and others have addressed with compliance to the highest safety standard, ASIL-D.
Second life for EV batteries
Wireless BMS also makes it easier for repurposing the battery for a second life, which is a benefit for the environment. Without the wire harnesses, it makes it much easier to replace and reuse the battery packs.
Lyne said specs like data health over the lifetime of the battery pack, the warranty of the battery pack and the efficiency of the battery pack—how long will it last—are all very important.
“A lot of vehicle companies rate their cars for eight years on the battery pack, but if you still get an efficiency of greater than 86% from that battery pack beyond the eight years, for example, up to 10 years, that is another two years of its life beyond what was originally hoped,” said Lyne. “That is a win-win for the customer and a win-win for the OEM that developed it, and it also means that you treated that battery pack well during its life.
“When you do fast charging of a battery pack today, that causes more stress in particular on the dielectrics of the cells, which may shorten the lifespan of a battery pack, but they still have to guarantee it for eight years,” he added.
“When the battery pack gets below 86% efficiency in an automobile, you are no longer guaranteeing the range that it was originally specified for—150 miles, 200 miles or whatever it is—for a typical driving condition at 55 miles per hour, and so it starts degrading, and what they want to do is to replace the cells or replace the entire battery pack,” Lyne said.
It is at this point when lithium-ion batteries for EVs get repurposed for a second life. They can be reused in a variety of applications, from backup systems for servers to residential solar panels.
It is still important that the battery pack has a warranty or guarantee for these industrial applications, which is where the battery-monitoring data or SOH also comes into play to indicate the performance of the battery.
The article originally published in EE Times EV Power special report.
Advertisement
Learn more about Analog DevicesRenesas Electronics AmericaTexas Instruments