Microelectronics play a crucial role in the modern healthcare landscape, enabling the development of smaller, faster and more energy-efficient devices. Wearable medical devices, driven by microelectronics, offer enhanced convenience and effectiveness in addressing various health issues.
As medical technology advances, the integration of microelectronic devices becomes increasingly prevalent. Devices like hearing aids, pacemakers, defibrillators and other medical machines continue to shrink in size while improving in efficiency. The marriage of microelectronics and healthcare exemplifies the industry’s commitment to making medical solutions more convenient and less intrusive for patients.
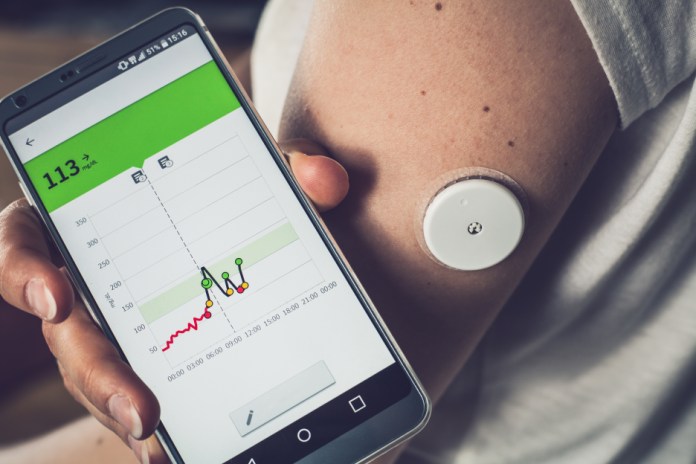
Wearable medical devices, driven by microelectronics, offer enhanced convenience and effectiveness in addressing various health issues. (Source: Adobe Stock)
The challenge of cleaning small-scale electronics
However, for electronics manufacturers, these compact devices bring about substantial challenges, particularly in the realm of cleaning their internal miniaturized printed-circuit boards (PCBs) and other electronic components. Ensuring the cleanliness of these components is crucial to prevent performance issues and potential failures. In this context, advanced cleaning methods and fluids play a pivotal role.
The electronics within medical devices must undergo meticulous cleaning and drying to eliminate production contaminants like fingerprints, dust and flux residues. Neglecting to remove these contaminants can compromise the device’s functionality and lead to inconsistent outcomes or catastrophic failures.
The PCBs found in today’s wearable medical devices are densely populated to maintain a small, lightweight and discreet form factor. Components like land-grid array (LGA) and quad-flat no-lead (QFN) packages have tight standoff heights that often trap moisture, making cleaning and drying these miniature PCBs a formidable task. Consequently, electronics manufacturers require effective cleaning fluids and methods to address these challenges.
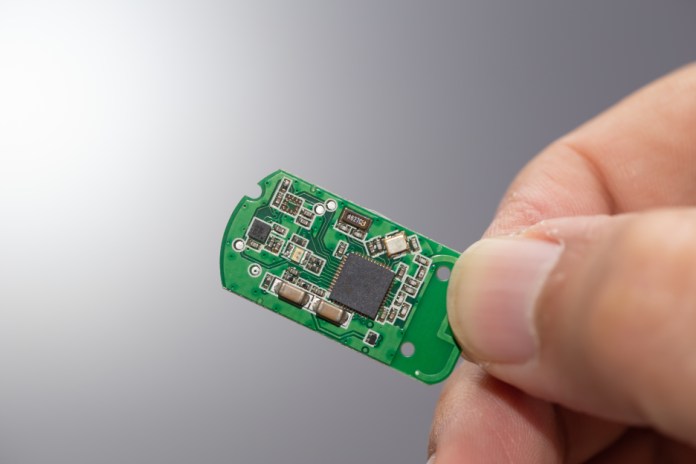
Ensuring the cleanliness of micro components is crucial to prevent performance issues and potential failures. (Source: Adobe Stock)
Resurgence of vapor degreasing
An effective method that has experienced a resurgence in popularity for PCB cleaning is vapor degreasing. This cleaning process, widely used in the past, fell out of favor in the late 1990s due to environmental concerns. However, advancements in solvent technology have led to the development of more environmentally friendly cleaning fluids, renewing interest in vapor degreasing for PCB cleaning.
How vapor degreasing works
Vapor degreasing operates within a closed-loop system consisting of two chambers: the boil sump and the rinse sump. The boil sump contains a specially engineered low-boiling, non-flammable cleaning fluid. PCBs and components are immersed and cleaned within the heated fluid. Once cleaned, they are mechanically transferred to the rinse sump for a final rinse and dry in more pure, uncontaminated fluid or inside the fluid vapors themselves. This results in clean, dry, spot-free components immediately ready for the next manufacturing step.
The absence of moisture is particularly appealing to medical device manufacturers, as it reduces the risk of bioburden, contributing to a more sterile product.

Vapor degreasing results in clean, dry, spot-free components immediately ready for the next manufacturing step. (Source: MicroCare, LLC)
Efficiency and consistency
Using a vapor degreaser not only ensures effective cleaning but also offers manufacturing efficiencies. The entire vapor degreasing process takes only six to 20 minutes and does not require additional drying or cooldown steps, saving valuable production time.
Once set up, the cleaning fluid inside the vapor degreaser remains chemically stable for thousands of uses, requiring minimal maintenance. This stability ensures consistent and repeatable cleaning results, simplifying the adherence to process validation specifications.
Documented results for validation
The vapor degreasing process is consistent, allowing for easy auditing and documentation for validation purposes. A complete cleaning record of each batch can be maintained, providing evidence that all steps defined by procedures and instructions were undertaken as expected.
The daily operation of a vapor degreaser is simple and can often be automated, simplifying worker training and ensuring qualified personnel can consistently conduct the part-cleaning procedures correctly.
Sustainable and compatible
Modern vapor degreasing fluids offer excellent materials compatibility, making them suitable for delicate PCBs or mixed-material devices. These fluids have low surface tensions and high liquid densities, enabling them to penetrate complex geometries and clean thoroughly around and under tightly packed PCB components.
Furthermore, the lower boiling point of these fluids reduces energy consumption, resulting in lower carbon emissions and less greenhouse gas output, contributing to sustainability goals.
Water and energy savings
There are significant resource and energy savings with vapor degreasing, especially when compared with aqueous cleaning. Aqueous systems require hundreds of gallons of non-renewable water. They also generate a wastewater stream that requires expensive treatment.
Additionally, water needs substantial amounts of electricity or natural gas to heat the water to an elevated temperature for cleaning. And because aqueous cleaning machines are bigger than vapor degreasers, they consume more energy to run.
By contrast, a typical vapor degreaser will use approximately 30 A of power when cleaning with many of the smallest machines using standard household electrical connections. When compared with water-cleaning systems where power consumption is measured in hundreds and thousands of amps and that often require 440-V circuits and large power panels to manage the electrical load, vapor degreaser energy savings are extensive.
The cleaning of microelectronics in medical devices, particularly wearable technology, is a critical aspect of the manufacturing process. Vapor degreasing has emerged as a reliable and efficient method, providing consistent and repeatable cleaning results while meeting sustainability requirements. As the healthcare industry continues to embrace the potential of microelectronics, ensuring the cleanliness and reliability of these small-scale devices will remain paramount for the well-being of patients and the advancement of healthcare technology.
About the author
Elizabeth Norwood is a senior chemist at MicroCare, LLC, which offers precision cleaning solutions. She has been in the industry for more than 25 years and holds a B.S. in chemistry from the University of St. Joseph. Norwood researches, develops and evaluates cleaning-related products. She currently has one patent issued and two pending for her work.
Advertisement