Overvoltage protection of AC power lines is a common practice, which encompasses a variety of protection circuit solutions. Most designs are cost-driven and tend to use only the bare minimum of protection strategies. Billions of low-cost metal-oxide varistor (MOV) devices are sold annually to meet these needs. For other designs requiring protection schemes that minimize warranty returns or to satisfy other product line cost issues, new hybrid devices that combine a gas discharge tube and MOV into single-package solutions are available along with power transient voltage suppressor (TVS) diodes. These devices offer enhanced protection capabilities that deliver greater reliability. In many cases, the greater initial cost will be offset by after-sale maintenance and warranty savings.
There also exists a class of applications in which failure is not an option. In many such applications, the cost of repair or replacement is driven by the cost to access the equipment — not the value of the equipment itself. Examples include tower-mounted and pole-mounted lights, signage, cameras, and communications equipment. In other applications, equipment failure simply cannot be tolerated. These may include emergency communications, military and medical equipment, critical 5G picocells, and security systems.
This article introduces a novel protection circuit designed to meet the requirements of this critical class of applications.
The voltage clamp trap
Circuit protection designers must ensure that the voltage ratings for the AC-input components will not be exceeded by an incoming voltage surge. Virtually all conventional overvoltage protection strategies for AC power lines use voltage clamping devices. Regardless of core technology, voltage clamps present a small but real resistance to the surge current, meaning that higher surge currents will drive higher let-through clamping voltages. (Figure 1 shows the characteristics of typical MOV devices.) This means that there will always be some level of surge current that may result in damaging clamping voltages.

Figure 1: Typical 10-mm MOV voltage-current characteristic curves. Click for a larger image. (Source: Bourns, Inc.)
The tendency is to choose a low-voltage rating to yield the lowest clamping voltage. However, the protection device must never conduct during normal power line voltage variations, which can exceed 20% of the line voltage. Operating in a continuous-conduction mode essentially ensures destruction of the protection component, as these components are traditionally only rated for transient conditions.
These competing requirements present a real challenge to the designer. In critical applications, the solution is often to select line input components with very high voltage ratings, with a corresponding increase in cost for those protection components.
Electronic current limiters to the rescue
Electronic current limiters (ECLs) use depletion-mode (normally “on”) MOSFETs in a two-terminal bidirectional integrated circuit that sense the passing current. These devices can switch “off” in about a microsecond when the current exceeds the rated trip current. Once tripped, the internal FET devices remain in the “off” state until the next voltage-zero crossing, at which point it reverts back to the low-resistance “on” state. In the “off” state, the ECL can withstand several hundred volts.
If an ECL, such as a Bourns TBU high-speed–protector (HSP) transient blocking unit device, is coupled with a small TVS diode (see Figure 2), the TVS device begins to conduct when the TVS threshold voltage is exceeded. This causes current to flow in the TVS device, which, in turn, trips the ECL. This action disconnects the protected circuit from the AC source precisely at the TVS breakdown voltage. This protection voltage level is independent of the magnitude of the surge voltage.

Figure 2 shows a typical protection circuit using an ECL and TVS device combination. Click for a larger image. (Source: Bourns, Inc.)
Implementing this type of exact and ensured voltage limit to the downstream AC-input components allows the protection designer to minimize the voltage ratings of those components, likely saving costs while being assured of effective protection.
Load overcurrent protection
The ECL can also be tripped by excessive current flow to the protected circuit. This may be caused by a fault in the protected circuit (not caused by an overvoltage event) that can be permanent or temporary. In this scenario, the ECL acts as an automatically resetting line fuse. As long as the fault persists, the ECL will be tripped at every half-cycle of the AC-input voltage, preventing excessive power to flow downstream.
An ECL can also function as a soft-start controller, limiting the peak inrush current during power supply startup, thereby reducing the stress on rectifier diodes, filter capacitors, and other AC-input components.
Voltage swell protection
If the AC-input voltage swell reaches dangerous levels, the TVS diode will begin to conduct just as it would during a transient event, preventing voltages exceeding the design limit from reaching the protected circuit. This can occur every half-cycle for as long as the voltage swell event persists. Because the ECL is fully conducting right up to the moment the voltage limit is exceeded, current is still allowed to flow to the protected circuit. In many cases, the protected circuit will draw enough power in each half-cycle prior to an ECL device shutdown to allow the application to continue to function normally. As soon as the swell condition ends, the ECL will remain in the “on” state until the next AC swell or transient event occurs.
Unlike simple voltage clamp protection circuits, this circuit will not only tolerate AC line voltage swells but will also protect downstream components from the higher voltages. In many cases, this circuit design approach will even allow the application to function normally during the voltage swell event.
Managing primary overvoltage
The circuit described above effectively manages the voltage and current delivered to the protected circuit. Consideration, however, also needs to be given to “primary protection,” meaning protecting the ECL device from voltages that exceed the datasheet limits without interfering with the protection provided by the ECL + TVS device combination.
Another source for overvoltage events is the triggering of the ECL itself. When powered from an inductive source, which is very common, the sudden interruption of current will cause the input voltage at the output of the inductor (transformer, choke, etc.) to spike in order to maintain continuous current flow. These spikes are typically not long in duration, but they do represent a threat to the ECL if not managed.
For example, a Bourns TBU HSP rated to withstand 850 V can be selected for AC powerline service, thereby setting the maximum clamping voltage. The TVS breakdown voltage sets the lower limit of the primary protection breakdown voltage. Using this combined approach helps ensure that the primary protection will be inactive at acceptable voltage levels while still providing needed protection for the ECL device.
Power loss management
Consideration should be given to the power loss in an ECL. For instance, an ECL deployed to protect a 125-VAC application consuming 100 W with a power factor of 0.8 would have an input current of 100 ÷ 125 ÷ 0.8 = 1 Arms. Using a 3-Ω ECL device would lead to a 3-W power loss. Of course, no one wants to see a 3% power loss in their protection scheme, but in “failure is not an option” applications, this is likely tolerable. (Note that 240-VAC applications would have half the current and one-fourth of this loss.)
Figure 3 shows an implementation of this circuit designed for the scenario above. The TVS diode is first selected to tolerate a 15% voltage swell above 125 VAC, which has a peak voltage of 125 × √2 × 1.15 = 203 V.

Figure 3: For this circuit, the Bourns Model SMCJ180CA TVS diode is a good choice with a breakdown voltage between 201 and 222 V. The desired 3-Ω ECL resistance can be achieved with four parallel Bourns TBU HSP Model TBU-CA085-500-WH devices, resulting in a trip current of about 2 A. Click for a larger image. (Source: Bourns, Inc.)
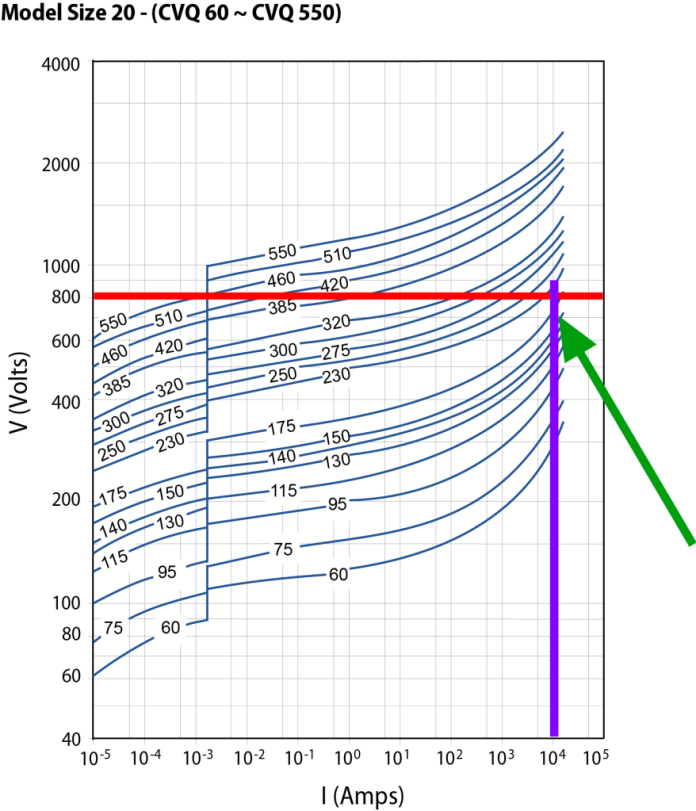
Figure 4: The prescribed overvoltage protection using a Bourns Model CVQ175K20 MOV device (green arrow). This solution will keep voltages well below 800 V (red line) during surge events up to 10,000 A (purple line). Click for a larger image.(Source: Bourns, Inc.)
Protection with confidence
Using the types of components in the novel circuit protection design presented in this article gives design engineers the confidence they need in protecting their AC power line–based applications to survive virtually any imaginable real-world line voltage swell or surge.
Advertisement
Learn more about Bourns
One thought on “A novel protection circuit design for AC power lines”