The Technical Committee of the Automotive Electronics Council (AEC) has expanded the scope of AEC-Q200, Stress Test Qualification for Passive Electrical Devices. The new Revision E has been published, which, among other passive components, now covers fuses.
The expansion of electrification in automotive devices (Figure 1) increases circuit-protection requirements; fuses provide the necessary overload protection. Revision E removes the ambiguity of test requirements among manufacturers of fuses and ensures that AEC-Q200–qualified fuses meet a high standard for ruggedness and reliability. This article describes the AEC-Q200 Standard and the new Revision E.
AEC background
Chrysler, Delco Electronics (General Motors) and Ford representatives met in January 1993 to discuss creating common qualification and quality system standards for electronic components. At the time, the automotive market was a smaller percentage of the total electronics market and received less attention from the manufacturers (how times have changed!). The representatives formed the AEC and created two committees: the Quality Systems Committee and the Technical Committee.
The Quality Systems Committee is no longer active, as quality specifications are now covered by the International Automotive Task Force’s Standard IATF 16949, an automotive quality system standard based on ISO 9001. The Technical Committee creates the qualification standards for components, manufacturing processes and test methodologies. The standards define the minimum set of tests that a component must pass to be qualified for use in automotive electronic applications.
The initial work of the Technical Committee began on a standard for stress testing of integrated circuits to ensure device reliability in the automotive environment. This effort resulted in AEC-Q100, Stress Test Qualification for Integrated Circuits. The AEC has since added AEC-Q101 for discrete semiconductors and AEC-Q200 for passive components. The AEC has expanded its membership to include automotive equipment suppliers and electronic component manufacturers.
AEC-Q200
The AEC-Q200 Specification, Stress Test Qualification for Passive Components, has evolved over the years and has been at Revision D since June 2010. Components covered by the standard include various types of resistors and capacitors, inductors, transformers, resonators, crystals, resettable fuses (PTCs and NTCs), thermistors and varistors. Depending upon the component type, qualified components must be capable of operating over a minimum temperature range of –40°C to 85°C; however, manufacturers can qualify their components to the specification’s specified temperature range.
There are two main stress categories that components must pass: environmental stresses, such as temperature cycling and humidity bias, and physical characteristic stresses, such as machinal shock and vibration. It is important to note that not all stresses apply to a particular technology.
AEC-Q200 is divided into component technology tables that list the stresses and may include additional requirements pertaining to that stress. Figure 2 visualizes the different stresses in each of the categories. The components must maintain their specifications under pre-test and post-test conditions, as shown in Figure 3.
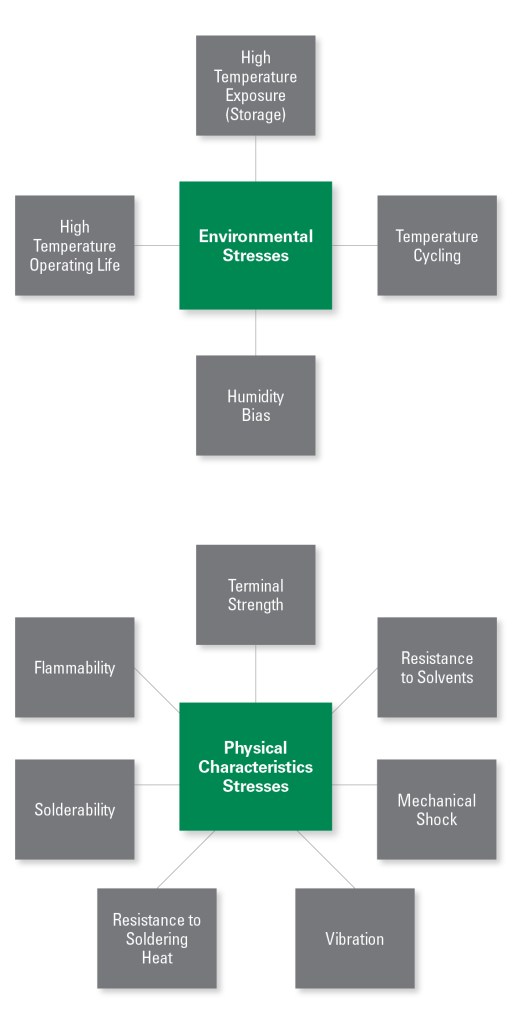
Figure 2: Categories of environmental and physical characteristic stresses (Source: Littelfuse Inc.)
New AEC-200 Revision E
This year, along with many technical changes, clarifications and editorial updates, the AEC has published Revision E of the AEC-Q200 standard to include fuses. Fuses provide necessary overcurrent protection for all the circuits in a vehicle, and fuses should meet the rigorous standards for use in automotive equipment that other passive components similarly must meet.
Littelfuse has contributed to the development of Revision E and the framework for defining the test requirements for fuses. The newly added Table 15 in AEC-Q200 lists the tests for fuses and additional requirements needed to comply with the AEC-Q200 Revision E standard. The table below shows a compressed version of Table 15.
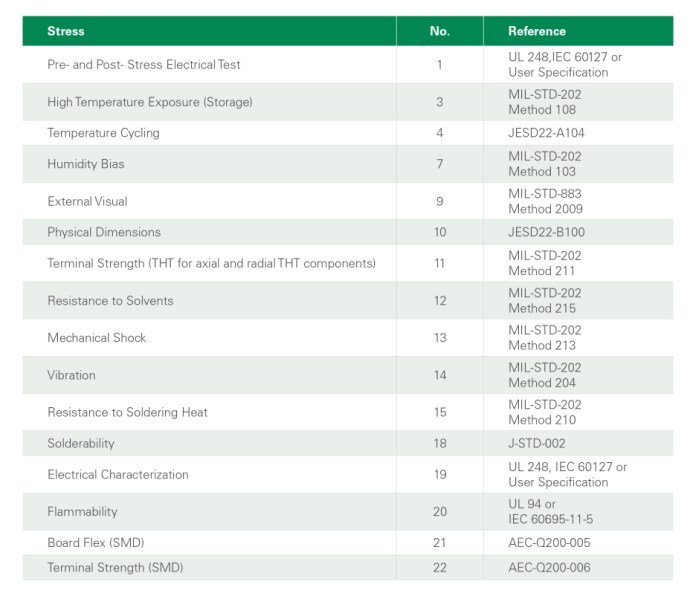
Table 1: AEC-Q200 qualification fuse stress tests and the reference for the test methodology (Source: Littelfuse Inc.)
Improved reliability for automotive fuses
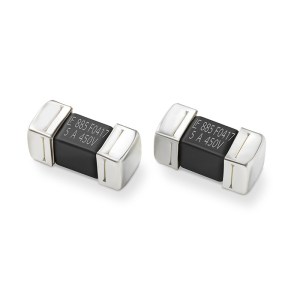
Figure 4: One example of an AEC-200–qualified fuse is Littelfuse’s 885 series Nano2. (Source: Littelfuse Inc.)
AEC-Q200 Revision E now provides a single standard that manufacturers can use to design and test fuses for the automotive market. AEC Technical Committee members who are experts in fuse technology and testing have thoroughly reviewed Revision E. Design engineers developing systems for automotive vehicles will be able to select AEC-Q200–qualified fuses that have been subjected to an extensive set of tests to ensure a rugged and reliable product.
As a result, designers can be confident that their overcurrent protection components now meet the same uniform AEC-Q200–qualification methodology that other passive components meet. Therefore, designers can now select from a full complement of AEC-Q200–qualified passive components to develop reliable products for the automotive industry.
References
Automotive Electronics Council. (March 30, 2023). “AEC-Q200 Revision E Stress Test Qualification for Passive Components.”
About the author
Saad Lambaz is the global standards manager at Littelfuse Inc. He is a member of the AEC-Q200 subcommittee as well as UL Standards and Engagement, IEC and other technical committees. He joined Littelfuse in 2014 after being involved in testing and certification services in his previous UL role. Saad’s current responsibilities include third-party component certification, standards development and representation of Littelfuse in local and global technical committees. He received his BSEE from Southern Illinois University. Saad can be reached at SLambaz@Littelfuse.com.
Advertisement
Learn more about Littelfuse