Scientists at research institute CEA-Leti, in collaboration with researchers at Politecnico di Milano, have claimed the smallest MEMS gyroscope that is capable of providing navigation-grade performance. The new MEMS gyroscope measures 1.3 mm2, achieved by leveraging nano-resistive sensing, and reportedly offers best-in-class bias stability and angular random walk (ARW) performance, together with a high resonant frequency.
The new gyroscope design is based on CEA-Leti’s nano-MEMS (NEMS) technology, using piezo-resistive nano-gauges for rotational speed and drive detection. The researchers have demonstrated that the NEMS-based gyroscope can deliver navigation-grade performance thanks to its high scale factor, quadrature compensation, accurate demodulation phase, and minimization of parasitic effects, which contribute to low noise and improved stability.
Low-power MEMS gyroscopes are used in every-day devices to monitor and control device position, orientation, direction, angular motion and rotation, said researchers. “With the growing development of driver-assist systems and other automated functions, the need for improved performance and robustness has increased significantly, fueled by the demand for miniaturization and cost control for real inertial navigation systems.”
Gyroscopes and accelerometers are integrated into inertial measurement units (IMUs). The IMUs use a combination of these devices, depending on the application, and are calibrated for different application grades.
To meet new requirements for high-performance IMUs, gyroscopes need to be navigation-grade. This means improved characteristics of one or two orders of magnitude compared to the best commercial MEMS gyroscopes, said CEA Leti, thus requiring a bias instability well below 0.1°/h and an ARW of less than 0.01°/√h.
The researchers said they reached these targets, demonstrating performance that matched the best state-of-the-art technology on ultra-miniaturized MEMS gyroscopes. The results were reported in a paper entitled 1.3 mm2 Nav-Grade NEMS-Based Gyroscope in the Journal of Microelectromechanical Systems.
One key feature noted in the report is the scale-factor values can be independently programmed by trimming the bias current flowing through the NEMS gauges. This eliminates the requirement for high voltages, typical of capacitive technologies, which increase capacitive couplings and generate unwanted tuning, resulting in undesired drifts due to second-order effects, such as tuning changes due to voltage drift and coupling changes due to parasitic drifts, according to the report.
In addition, the high-sensitivity of the NEMS gauges are achieved through an optimized electromechanical design and use of high gauge biasing currents in the order of a few hundred µA.
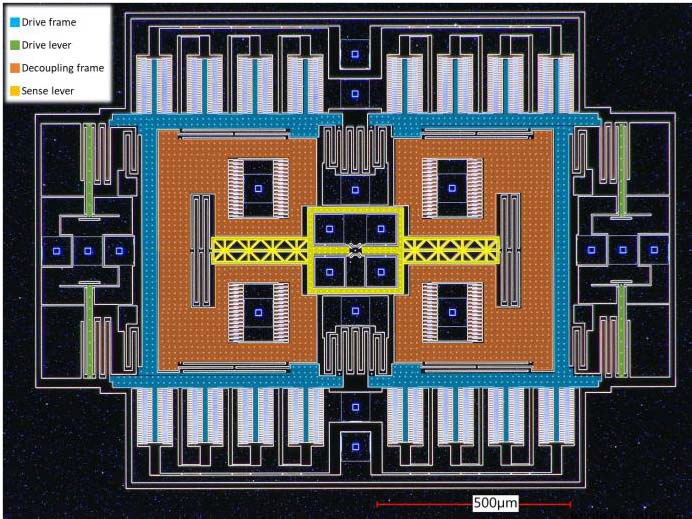
Top-view of the gyroscope with false colors highlighting the drive and Coriolis frames and the corresponding decoupling levers (Source: CEA-Leti)
Leveraging CEA-Leti’s expertise in highly sensitive sensors based on the silicon nano-gauges and Politecnico di Milano’s expertise in gyroscope design, the new gyroscope solution achieves 0.004°/√h ARW and 0.02°/hr stability on average over several tested samples, which is reportedly unrivaled for a 1.3 mm²-size gyroscope footprint, the paper reported.
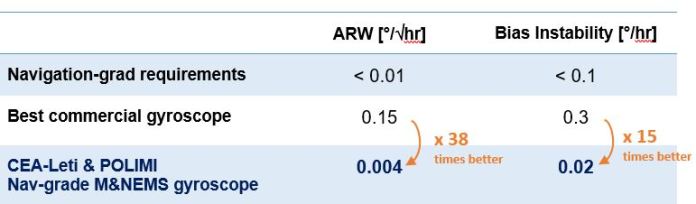
Comparison of CEA-Leti’s navigation-grade MEMS gyroscope performance vs. best commercial gyroscopes (Source: CEA-Leti)
The ARW and bias instability performance were highlighted on non-static operations and achieved without Kalman filter compensation, according to researchers. “After nine-minute long in-operation navigation where the gyro is repeatedly tilted by 180° constant angle rotations and by AC random motion with about 200-dps peak-to-peak value, the residual angle error at the end of navigation corresponds to only 0.07°.”
In addition, to address a range of applications (short-term navigation in a GPS outage, indoor navigation, platform stabilization, accurate robotic motion control for Industry 4.0, guided munitions, etc.), the MEMS gyroscope provides a resonant frequency greater than 25 kHz to withstand conventional vibration environments.
“This improved performance must not come with a high cost so the device will be priced competitively in large-volume markets, such as the automotive and consumer markets,” said Philippe Robert, MEMS business development manager and senior expert at CEA-Leti, in a statement. “The size of these new gyroscopes must therefore not exceed 2 mm² per axis, while maintaining standard MEMS technology and using wafer-level vacuum packaging.”
To keep manufacturing costs low, the team said it focused on both the sensor’s size and the robustness of the fabrication process, especially on vacuum-WLP. The MEMS-based gyroscope is fully compatible with standard MEMS foundries for high-volume markets such as the automotive industry, according to researchers.
Manufactured on CEA-Leti’s silicon pilot line, these gyroscopes can be co-integrated with high-performance three-axis accelerometer and barometric-pressure sensors. Researchers believe this technology can reach markets within two years thanks to its compatibility with most MEMS foundry processes.
CEA-Leti’s and Politecnico di Milano’s gyroscope technology has more than five patents and CEA-Leti’s M&NEMS platform has more than 25. The researchers said they will continue to work on achieving better performance, integration, and cost.
Advertisement