Consumers enjoy the benefits of today’s new smart appliances, which include more intelligent convenience features and IoT-based interfaces that allow them to control their home environment. These products range from air fryers to robotic vacuum cleaners that save the consumer time when doing various chores and preparing food and drink.
Designers must incorporate smart technologies into their new appliance designs to satisfy consumer demand. They must also make the appliances energy-efficient so that battery-operated products can operate with longer intervals between downtime and recharging.

Figure 1: Small appliances are getting smart, and many now include IoT-based interfaces. (Source: Littelfuse Inc.)
The greater the appliance’s electronic content, the greater the designer’s challenge is to ensure the product is robust and reliable against electrical hazards, such as overvoltage transients, overcurrent conditions and electrostatic discharge (ESD). This article introduces designers to circuit protection schemes and some unique components that protect circuits from electrical hazards. The article also recommends components to reduce power consumption for energy savings. All of these components will allow the designer to develop a safe, efficient, robust and smart small appliance.
Recommended components
Figure 2 illustrates a few examples of smart small appliances, along with components used for circuit protection, to maximize efficiency and detect the machine’s state. These components protect the circuits from electrical hazards, such as overcurrent conditions and overvoltage transients. In addition, specific components will detect overtemperature conditions and improperly positioned parts of the appliance. Some components will also contribute to higher-efficiency appliances.
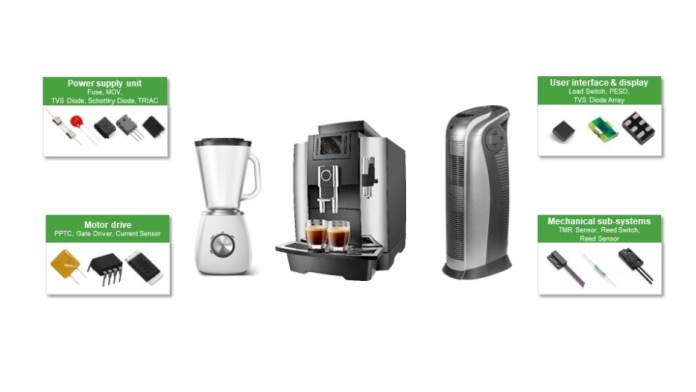
Figure 2: Small appliances and components recommended for safe and efficient operation (Source: Littelfuse Inc.)
Block diagram of a typical small appliance
Figure 3 breaks down an example home appliance into individual circuit blocks. These circuits include AC/DC power conversion, microprocessor control, motor drive, heating, manual controls and a display. The table in the figure highlights recommended component types for the circuit blocks requiring circuit protection, efficient operation and sensing.
Protecting circuits from electrical hazards
Protection components for the AC input primary protection circuit
AC-line-powered products must contend with the AC line’s voltage transients and high-current capacity, typically 15 A for a 120-VAC line in North America. The AC input primary protection circuit must protect downstream circuit blocks from overcurrent conditions and voltage transients.
Time-lag fuses are used to protect the circuits from an overcurrent, such as a short-circuit. Due to the product’s inrush current, a time-lag fuse will avoid nuisance fuse openings. Ensure that the selected fuse has a voltage rating that exceeds the voltages in single-phase worldwide power-line circuits. Also, ensure that the fuse’s interrupting rating exceeds the current rating for typical worldwide single-phase AC power lines. To enable product sales in all regions of the world, consider a fuse that complies with IEC 60127-2.
AC power lines are susceptible to overvoltage transients that can strike products such as appliances connected to an AC line. Transients include lightning induced on power lines. Large motors switching on and off also induce transients. Using a metal oxide varistor (MOV) after the fuse and in parallel with the AC line will protect downstream circuitry. Select an MOV with:
- Peak current absorption from a single transient pulse of at least 4.5 kA
- Operating temperature rating of up to 105°C
- Ability to survive a 6-kV/3-kVA wave surge in compliance with Annex G of IEC 62368-1
Protecting the AC/DC power supply
Portions of transients that get through the MOV due to their non-ideal response time can damage downstream components. In addition, ESD can damage integrated circuits (ICs). Protect the AC/DC power supply with a transient voltage suppressor (TVS) diode from overvoltage conditions. Key features of TVS diodes include:
- As much as 600 W of pulse power absorption
- 30-kV withstand voltage from ESD strikes, in compliance with IEC 61000-4-2
- Fast response time of under 1 ps
- Bidirectional and unidirectional models
- Space-saving surface-mount packages
Protecting the motor control circuit
The appliance motor needs protection from damage due to short-circuits, mechanical overloads and overheating. Consider a polymeric positive temperature coefficient (PPTC) device, a resettable fuse for short-circuit protection. Ensure the PPTC fuse is rated for operation in excess of the circuit’s maximum voltage. Look for models that hold current capacities of at least 2 A and fast trip times under 30 seconds. A good PPTC fuse will be compliant with EN 60730-1.
To prevent motor damage from mechanical overloads and overheating, monitor motor current with a current-sense resistor. Use a current-sense resistor with as low a resistance as possible to minimize power loss in the motor control circuit. Sense resistors are available with resistances that range from 1 mΩ to 56 mΩ. Tolerances can be 1% for accurate current measurements, and the sense resistors can save PC board space with surface-mount packaging.
Heating assembly protection
To avoid damage in appliances that heat liquids, include a sensor to monitor the liquid temperature. This ensures the appliance will not be exposed to damaging high temperatures. Consider an NTC thermistor that can reside in a stainless-steel probe housing or a customized solution for a liquid temperature probe.
The display block: backlight LED driver and LED/LCD display
The display block communicates and receives data from the microcontroller (MCU). To maintain error-free data between the MCU and the display circuit, use a TVS diode to protect the ICs from ESD. TVS diodes can have low clamping voltages to ensure the safety of the ICs in the circuit. As with the TVS diodes recommended for the AC/DC power supply, models can absorb as much as a 30-kV ESD strike. In the display circuits, 200-W peak pulse power absorption capacity and less than 1-ns response time are sufficient. Choose from unidirectional or bidirectional versions and take advantage of surface-mount packaging.
Consider a TVS diode array as an alternative to a single TVS diode, which can protect two data lines and reduce component count. Figure 4 illustrates a two-line TVS diode array with a Zener diode for ESD protection. This TVS diode array offers a low capacitance of about 0.2 pF per I/O signal line. The array consumes minimal power with a leakage current of 10 nA.
Mechanical subsystem: position/level detection and keypad
Ensure that fluid levels are at appropriate levels and that lids or chambers are correctly closed for the safe operation of the appliance. One level and proximity detection solution is a tunneling magnetoresistance (TMR) sensor. Figure 5 shows a TMR sensor with an active power drive. TMR sensors offer the benefits of excellent sensitivity, 17 G and ultra-low power consumption, drawing only 1.5 µA at supply voltages from 1.8 to 5.5 V. TMR sensors have an exceptionally long life of up to 20 billion cycles. The sensor also has an environmental rating of IP67 against ingress from moisture and dirt.
As an alternative for position sensing, consider a reed switch. A reed switch does not consume any power. Versions are hermetically sealed and can switch up to 10 W at either 200 V or 0.5 A. A third option, depending on the type of small appliance, is a snap-action switch. A snap switch is the simplest of the three sensor types to implement position detection. This type of mechanical switch can have a contact rating of 3 A at either 125 VAC or 24 VDC. Operating life can range from 10,000 cycles at 3 A to 300,000 cycles at 0.1 A.
These protection and sensing components can help ensure a robust and reliable appliance design. Furthermore, the recommended components do not interfere with the primary circuitry that makes the product functional.
Designing efficiency in the appliance
AC/DC power supply
MOSFETs can maximize the AC/DC power supply’s efficiency by allowing the switch-mode power supply to operate at a high switching frequency. To obtain minimal power loss in the circuit, select a MOSFET with the following characteristics:
- Low RDS(on), below 450 mΩ
- Low gate charge, in the tens of nanocoulombs
- Fast slew rates with dV/dt values in the range of 50 V/ns
In the DC rectification stage, consider using Schottky diodes. An example Schottky diode package, shown in Figure 6, contains two legs of a full wave rectifier. An effective Schottky diode will have a low forward voltage drop under 0.5 V, low junction capacitance of about 84 pF and low leakage current under 14 mA.
Motor control circuit
Gate driver ICs provide efficient driving of MOSFETs or IGBTs. Gate drivers have low propagation delays, as well as fast rise and fall times to facilitate the high-frequency operation of power transistors. Versions can be single or dual drivers and source and sink at least 2 A.
AC switching circuit
In this circuit, an alternistor TRIAC can control an AC heater. The thermally robust component can operate with a junction temperature reaching 150°C. These components can carry 16 A to power the heater.
DC/DC converter
Consider using a low-power load switch for efficient power distribution to the MCU, display and mechanical subsystems (see Figure 7). The load switches should provide:
- Current delivery of up to 2 A
- Operating current of 1 µA
- On-resistance under 120 mΩ
- A typical quiescent current of 7 nA
- A 335-µs controlled rise time to mitigate the effects of inrush currents
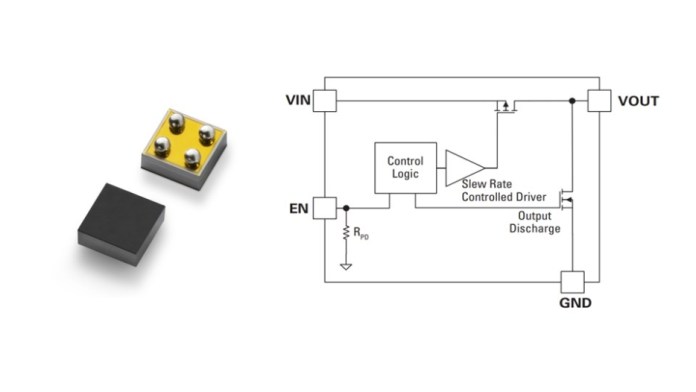
Figure 7: Load switch (Littelfuse LQ05022QCS4 protection IC) with slew rate control (Source: Littelfuse Inc.)
These components will enable the appliance to run with maximum efficiency. Low power consumption saves on annual utility costs for the consumer, and lower-power circuits contribute to longer-life appliances.
Protection against electrical hazards such as overcurrent, overvoltage, ESD and overtemperature is critical for ensuring reliable operation. The recommended components enable designers to develop safe, reliable and low-power-consuming small appliances.
To ensure a robust and efficient product, designers should take advantage of the component manufacturers’ application engineers to save design time and compliance costs. The application engineers can help with the selection of cost-effective protection, sensing and high-efficiency components. They are also knowledgeable of the applicable safety standards for the different appliances.
Component manufacturers such as Littelfuse can perform pre-compliance testing to avoid compliance test failures and save on delays and added costs for multiple compliance test cycles.
Collaborating with the component manufacturer’s application engineers and using the recommended components will also help to produce robust, reliable and efficient smart small appliances.
References: standards
- IEC 60127-2 Ed. 3.0 b:2014 – Miniature fuses – Part 2: Cartridge fuse-links (ansi.org)
- IEC 62368-1 Ed. 1.0 en:2010 – “Audio/video, information and communication technology equipment – Part 1: Safety requirements” (ansi.org)
- IEC 61000-4-2 Ed. 1.2 b:2001 – Electromagnetic compatibility (EMC)- Part 4-2: Testing and measurement techniques – Electrostatic discharge immunity test (ansi.org)
About the author
Paulius Juskevicius is a strategic marketing manager for the electronics business unit at Littelfuse. He joined Littelfuse in 2016 as a field application engineer for the EMEA region. His current responsibilities include managing marketing activities for new product launches and performing marketing studies and feasibility analyses for new product ideas. Juskevicius earned his master’s in electrical engineering from Kaunas University of Technology.
Advertisement
Learn more about Littelfuse