The automobile industry’s two-pronged quest for better fuel efficiency and reduced CO2 emissions presents a number of technological problems for the sensor systems that support these platforms, as well as the battery management systems and all other parts of the engine. Electric vehicles (EVs) are benefiting from technological advancements, which are delivering lower prices while also providing the increased range efficiency that many consumers want. The market is being driven by a mix of higher-capacity batteries, more efficient electric motors, and innovative wide-bandgap (WBG) semiconductor solutions for the entire powertrain. WBG materials like gallium nitride (GaN) and silicon carbide (SiC) have exceptional inherent properties, offering a variety of system-level benefits for improved performance.
The powertrain system of an EV involves several solutions, from the on-board charger through the battery and its management system. Today’s battery drives the overall cost, and this is mainly determined by the cost per cell and its mechanical protection casing. The size of a battery is a compromise between battery life and cost: More cells mean more autonomy but are simultaneously more expensive.
The battery, DC/DC converters, on-board charger, and traction inverter are all contained in different enclosures in hybrid and electric powertrains. Designers may now integrate these systems utilizing a single domain controller and power stage. This helps them enhance efficiency and reliability while lowering costs as well as satisfying functional safety criteria.
Recommended
Designing with WBG semiconductors takes a little extra know-how
WBG Semiconductors for EVs
Manufacturers of EVs and hybrid EVs (HEVs) are looking for efficient power-conversion solutions for several powertrain stages. WBG semiconductors provide a performance edge over silicon in several respects: higher efficiency and switching frequency, along with the ability to withstand higher operating temperatures and voltages.
GaN has a bandgap of 3.2 electron volts (eV), approximately 3× that of silicon’s 1.1 eV. This indicates that it takes more energy to excite a valence electron in the semiconductor’s conductive band. Although this characteristic restricts GaN’s applicability in ultra-low–voltage applications, it does allow for higher breakdown voltages and thermal stability at higher temperatures.
Because more energy is required to excite a valence electron in the conductive band of the semiconductor, higher breakdown voltages, higher efficiency, and better thermal stability at high temperatures can be achieved. The main advantage of a SiC MOSFET is the low drain-to-source on-resistance (RDS(on)), up to 300× to 400× lower than that of silicon devices at the same breakdown voltage.
Smaller circuits and lower weight, as well as improved weight distribution and lower total power usage, are all advantages of employing SiC technology in inverters. This is due to the fact that SiC MOSFETs can operate at a considerably greater switching frequency, allowing many of the inverter’s circuit components to be smaller. SiC devices can also operate at greater voltages and currents than traditional silicon power semiconductors, resulting in increased power density and lower switching losses, even at high temperatures.
GaN and SiC solutions
To enable EVs to charge faster, automotive power electronics designers need GaN and SiC devices and a new powertrain architecture that can meet EVs’ efficiency and power density requirements. To obtain maximum driving range on a charge for the given battery capacity, the entire power-conversion chain must achieve the maximum efficiency possible. Batteries must have a very high energy storage density. The battery life of an electric car directly reflects the efficiency of its powertrain system.
GaN is an attractive substitute for silicon in the manufacturing of high-efficiency voltage converters, power MOSFETs, and Schottky diodes, as it substantially improves the efficiency of power-conversion stages. Compared with silicon, GaN offers important improvements, such as greater energy efficiency, smaller dimensions, lower weight, and lower overall cost.
Both GaN and SiC have a large bandgap. While these materials both work well, their properties, applications, and gate-drive requirements are all unique. In high-power and extra-high–voltage (above 650 V) applications, SiC transistors may compete with IGBT transistors. In power applications with voltages up to 650 V, GaN may compete with current MOSFETs and superjunction MOSFETs.

Figure 1: Silicon and WBG power semiconductor applications for the system power level as a function of operating frequency. Click for a larger image. (Source: STMicroelectronics)
The traction inverters in EVs demand power switches with current capability of several hundred amperes to support hundreds of kilowatts of power. These systems are a better fit for IGBTs or SiC MOSFETs. On the other hand, on-board chargers and HV-to-LV DC/DC converters, which are rated up to 25 kW, are a great fit for GaN.
SiC 1,700-V technology is a silicon IGBT substitute. SiC technology offers higher switching frequency while lowering system size and weight, whereas silicon forces compromises in circuit topologies, owing to switching frequency limits to avoid additional losses. The physical characteristics of SiC allow for an ideal physical structure for high-power electronics, improving the form factor in terms of weight and shape, which is critical for automotive applications.
By using two-level topologies with fewer components and easier control methods, Microchip Technology Inc.’s new SiC product line, the MSC035SMA170B series, solves the challenges of IGBTs. With no switching constraints, power-conversion devices may be smaller and lighter, allowing more charging stations to be installed and expanding the range and operating time of heavy-duty trucks, electric buses, and other battery-powered commercial vehicles.
Microchip highlights the main features for the new portfolio: stable threshold voltage, degradation-free body diode, smallest increase in RDS(on) overtemperature, unrivaled avalanche ruggedness, and short-circuit withstand times similar to IGBTs.

Figure 2: Microchip Technology’s SiC power solutions. Click for a larger image. (Source: Microchip Technology)
GaN is an extremely versatile semiconductor material that can operate at high temperatures and voltages, helping to efficiently meet a wide range of communications and industrial designs. One of the challenges in the field of EVs is the development of fast and efficient charging. GaN technology can offer fast charging that uses energy in a much more efficient way.
One example is Texas Instruments Inc.’s GaN FET solutions with integrated gate drivers that will double the power density while reducing the size by about 60% and enabling switching rates of up to 2.2 MHz. These GaN FETs not only have integrated gate drivers but also a temperature sensor that allows active power management to optimize the system’s thermal performance dynamically.
Due to different manufacturing technologies, “standard” FETs and their gate drivers are utilized independently in large-scale power systems. This is added to the parasitic inductance, which reduces GaN’s switching capability. Switching losses are greatly increased by common-source inductance.
Formula E requirements
Formula E is the only motorsport event to test the latest technologies in next-generation EVs. The heart of a Formula E vehicle is its power unit, the propulsion system, which consists of three elements: the battery, the inverter, and the motor. The inverter is the brain of the system. It is responsible for converting the direct current from the battery into a high-density alternating current that is sent to the engine. However, during deceleration, the regenerative motor brake is activated, and the current follows the reverse path.
Power density (or current per unit surface), weight-to-power ratio, and immediate full-power availability are all mandatory requirements in Formula E. One advantage is that there is more flexibility in the inverter’s design, due to the low-volume–production requirements and a more manual inverter assembly process.
Moreover, cooling fluid selection and cooling characteristics can be more freely chosen, and there is a higher allowed pressure drop in the cooling system.
As in many other applications, Formula E silicon IGBT modules have been progressively replaced with SiC MOSFET devices, a promising alternative technology. With low weight and enhanced efficiency as key factors, Formula E can benefit from the low losses of SiC MOSFETs in the inverter design.
As an example, Hitachi ABB Power Grids’ RoadPak 1.2-kV SiC MOSFET half-bridge module, shown in Figure 3, features a small footprint (<70 × 75 mm) and the latest-generation SiC MOSFET with low losses and high reliability to meet the increasing demand of the e-mobility market.
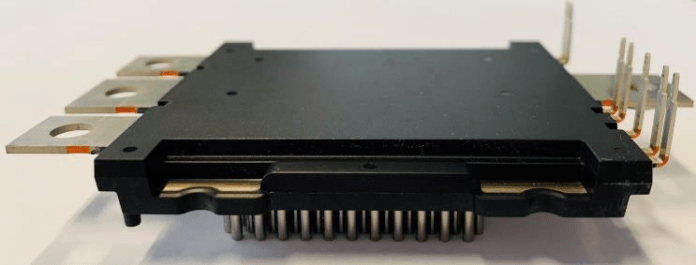
Figure 3: The Hitachi ABB Power Grids RoadPak 1.2-kV SiC MOSFET half-bridge module (Source: Hitachi ABB Power Grids)
The RoadPak baseline design for the EV market is based on eight parallel SiC chips, which can be increased to 10 without changing the outline. This is the most practical solution, as increasing the active surface of individual SiC chips is limited due to yield challenges in manufacturing. The active area of SiC MOSFETs currently in the market is less than 30 mm2.
Formula E is pushing the limits of power electronics technology, leading to a range of new SiC solutions. EVs will benefit from the new SiC power solutions by delivering simpler cooling systems, longer range, and better performance. They will also extend the battery life of the EV, and battery charging will be much faster with improved on-board chargers and DC/DC converters.
The numerous partnerships between chip companies and Formula E will benefit e-mobility with numerous engineering solutions not only from SiC chip manufacturers but also from GaN chip manufacturers.
Advertisement
Learn more about Microchip TechnologyTexas Instruments