Researchers at the University of California San Diego and California-based company ZPower have developed a flexible, rechargeable silver oxide-zinc (AgO-Zn) battery with a five to 10 times greater areal energy density than lithium-ion (Li-ion) batteries. The high-power energy density makes the rechargeable silver-zinc battery suited for next-generation consumer electronics, including IoT devices and wearables.
The breakthrough was achieved by leveraging a proprietary technology from ZPower and special inks and characterization techniques developed by UC San Diego’s nanoengineering team. Contributing to its lower cost and scalability, the battery is manufactured using a screen-print process under normal conditions, compared to most flexible batteries that need to be manufactured in sterile conditions under vacuum, according to researchers.
For the battery, the researchers used a proprietary cathode design and chemistry from ZPower, while the UC San Diego teams leveraged their expertise in printable, stretchable sensors, and stretchable batteries as well as advanced characterization for electrochemical energy storage systems.
The batteries also are customizable by size and capacity with an areal capacity of 50 milliamps per square centimeter at room temperature, which is 10 to 20 times greater than a typical Li-ion battery, said researchers. This translates into five to 10 times more power for the battery tested by researchers for the same surface area.
In addition to improving the battery performance, another focus of the research was to improve the manufacturing process by using a low-cost scalable production process, polymer-based flexible architecture, and customized ink formulations.
The team’s findings were published in the journal Joule. Lu Yin, one of the paper’s co-first authors and a Ph.D. student in the research group of UC San Diego’s nanoengineering Professor Joseph Wang, said in a statement that these “batteries can be designed around electronics instead of electronics needed to be designed around the batteries.”
“This kind of areal capacity has never been obtained before,” Yin stated. “And our manufacturing method is affordable and scalable.”
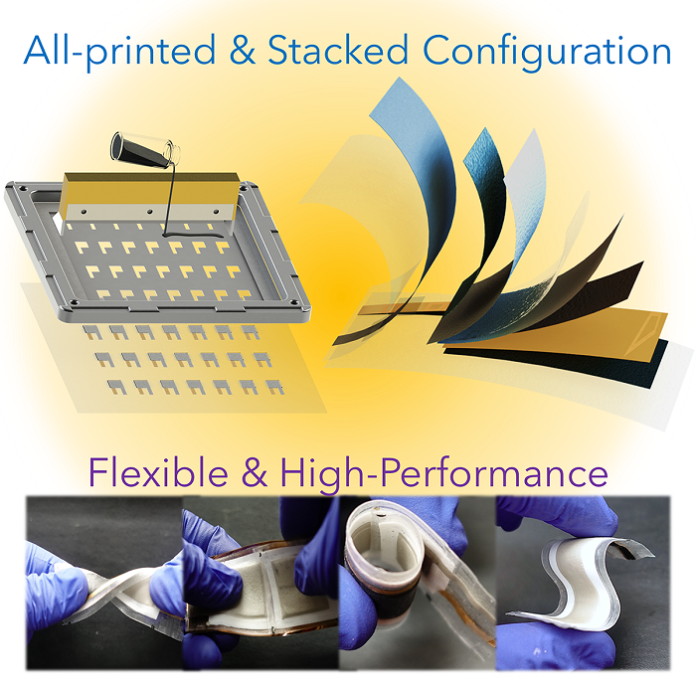
(Image:) University of California San Diego
The battery’s energy density is thanks to a AgO-Zn chemistry, unlike most commercial flexible batteries that use a Ag2O-Zn chemistry, which yields a limited cycle life of <50 cycles, low capacity (<12 mAh/cm2 for a primary cell and <3 mAh/cm2 for secondary cell), and high internal resistance (~102 Ω) that results in large voltage drop during operation, according to the UC San Diego research paper. These features have limited the applications for the silver-zinc batteries.
To address the limitations, researchers used a proprietary AgO cathode material. Although AgO is traditionally considered unstable, said researchers, ZPower’s AgO cathode material uses a proprietary lead oxide coating to improve the AgO’s electrochemical stability and conductivity. The AgO-Zn chemistry also gives the battery its low impedance. Further lowering the impedance is the battery’s printed current collectors that exhibit “excellent conductivity.”
The new battery has higher capacity than any of the flexible batteries currently available on the market, according to researchers, because the battery has a much lower impedance. “The lower the impedance, the better the battery performance against high current discharge.”
Impedance measurements during test of the electrochemical performance of the flexible AgO-Zn battery as a secondary cell (rechargeable) showed low impedances during cycling, according to the paper. Test results also indicated that the cycle life of the unstable AgO oxidation state can be controlled with a significantly increased cycle life compared to previous studies.
To determine the impedance of the batteries researchers used the direct current internal resistance (DCIR) method during cycling of the full-cell or a 3-electrode configuration with a Zn foil serving as the reference during cycling of the separated anode and cathode half-cells.
Researchers said the 3-electrode impedance results provided insight into possible approaches in improving the battery’s cycle life and performance. It also indicated that the impedance of the AgO cathode is responsible for the majority of the cell impedance.
Recommended
Spotlight: Search for the perfect battery finds many possibilities, few answers
To demonstrate the battery performance, researchers powered a flexible E-ink display system with an integrated microcontroller and Bluetooth modules that require pulsed high-current discharge. Findings indicated that the battery performed better than lithium coin cells and the printed battery cells were charged for more than 80 cycles without any “major signs of capacity loss.” In addition, they remained functional even after repeated bending and twisting.
But first the researchers needed to develop a new process to manufacture the batteries. One roadblock was finding the right ink formulation to make AgO viable for printing. AgO had never been used in a screen-printed battery because it is highly oxidative and chemically degrades quickly, according to researchers.
Once they developed the right ink formulation the battery could be printed in a few seconds and were ready to use in minutes. In addition, the battery could be printed in a sheet-to-sheet or roll-to-roll process, increasing the speed and scalability of manufacturing.
Researchers also developed printable and flexible separators and a solid-phase KOH-PVA hydrogel to enable a low-profile stacked sandwich configuration. The batteries are printed onto a polymer film with a high melting point (about 200°C or 400°F) that can be heat sealed. Current collectors, the zinc anode, the AgO cathode, and their corresponding separators each constitute a stacked screen-printed layer.
The fabrication and assembly process of the all-printed, flexible, and rechargeable AgO-Zn batteries can be used to manufacture different cell sizes with “adjustable” areal capacity, said researchers, enabling customizable battery form factors that are tailored for specific applications.
The team believes it has set a new benchmark for the further development of printable flexible batteries. Additional work will include further optimization of the fabrication process, the ink composition, and the layer thicknesses and porosities. Both the UC San Diego nanoengineering team and ZPower are working on a cheaper and faster charging battery for 5G devices and soft robotics.
Advertisement