As a design engineer working in the aerospace and defense (A&D) sector, how can you continue to provide higher power in your end design while simultaneously shrinking the size of your printed-circuit boards to achieve a smaller system size? You need power-dense, high-power DC/DC switching regulators on the front-end power rail.
A buck controller with external field-effect transistors (FETs) has typically serviced any power rail ≥24 V or higher that requires 6 A of output current or more than 80 W of total output power. While buck controllers offer both design flexibility and the ability to meet increasing power demands, they are no longer the only switching regulators able to meet the demands for higher power. A new generation of high-current (>6 A) converters with an integrated FET provides a more power-dense solution and a vast feature set targeted for high-performance end applications, with less design effort.
The advantages of increased integration
Controllers with external FETs give engineers the flexibility to meet the high-performance requirements of their designs and are often cost-efficient depending on inductor/FET selection. In contrast, high-current converters are a more integrated solution, providing an advantage when it comes to total solution size and ease of use without compromising efficiency or increasing electromagnetic interference (EMI). Table 1 compares these two device types for use in high-performance applications.
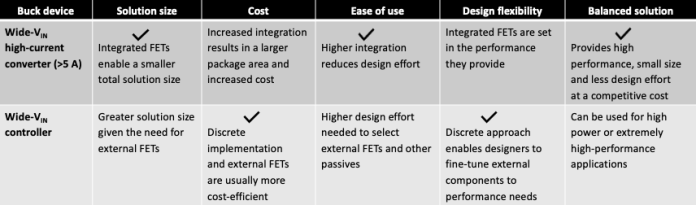
Table 1: Comparing wide-voltage high-current converters vs. controllers. Click for a larger image. (Source: Texas Instruments, Inc.)
Let’s review some significant parameters of interest in A&D designs.
Solution size
Since cost is usually not a large concern in A&D applications, high-current converters that pack high-efficiency silicon in extremely dense HotRod or Enhanced HotRod quad-flat no-lead packages can be an attractive alternative for engineers looking to shrink the size of their solution. Power density is an important consideration in A&D designs. You can typically expect to save at least 75 mm2 to 100 mm2 on average by using an integrated FET converter at a higher current instead of a controller. Overall solution size does depend on inductor selection, however.
While a controller will always offer better efficiency, a high-current converter such as the 36-V, 10-A LM61495 buck converter with an integrated FET provides the best balance between size and performance. Learn about how to do more with less in the white paper “Understanding the Trade-offs and Technologies to Increase Power Density.”
Adjustable switching frequency
Engineers who choose to work with high-current converters can still benefit from some flexibility, thanks to these devices’ adjustable switching frequency (from 200 kHz to 2.2 MHz). This wide switching-frequency range, coupled with low dropout performance, makes high-current converters suitable for one of the fastest-growing aerospace applications: USB Power Delivery (USB PD). USB PD applications typically have stringent power-dissipation requirements, with wide output-voltage ranges at low dropout where high duty-cycle conversion is necessary (21-V input to 20-V output conversion). The converter’s ability to operate at low switching frequencies provides a viable solution in terms of power dissipation.
Low EMI
Another important performance specification for consideration in both USB PD and most other A&D applications is EMI. Meeting EMI requirements at a system level is very important, and a switching regulator can be a large source of emissions. Typically, with higher device integration (optimized package construction, integrated bypass capacitors, etc.), a significant reduction in the input parasitic inductance formed from the input high-transient–current (di/dt) loop creates a low-EMI solution.
High-current converters also offer several features that help minimize common EMI challenges, including spread spectrum (pseudorandom and dual random), frequency synchronization, adjustable slew-rate control through the RBOOT pin, an adjustable switching frequency, and even integrated capacitors. These features, coupled with increased integration, enable high-current converters to meet low-EMI design requirements. Learn more about EMI mitigation techniques in the white paper “Time-Saving and Cost-Effective Innovations for EMI Reduction in Power Supplies.”
Conclusion
In high-performance applications such as A&D, test and measurement, medical imaging, and factory automation, increasing power requirements make high-performance, high-current converters such as the LM61495 an attractive alternative to controllers. Converters provide a balanced solution in terms of performance, integration, and power density and incorporate a vast feature set that provides further design flexibility for an integrated FET switching regulator while making it easy to meet stringent EMI requirements.
High-current converters provide many solutions to common power design challenges in performance applications. Of course, the choice of the switching regulator will always depend on your specific end application, but in a world where design requirements are constantly changing, you are no longer limited to a single device type.
Advertisement
Learn more about Texas Instruments