The challenge to improving speed and product yield in manufacturing and process control operations resides in control system intelligence. While advanced software technology and algorithm innovations provide the capability to realize Industry 4.0 efficiencies, the system hardware must operate reliably. If it does not, interruptions will slow manufacturing and control processes or negatively impact yield. Either situation causes increased costs. The programmable logic controller (PLC), the intelligence of the Industry 4.0 system, must have high reliability to achieve the benefits of Industry 4.0. Thus, PLCs need protection from current overloads, voltage transients, and electrostatic discharge (ESD).
This article guides electronics engineers and designers on the methods to improve reliability by offering components and techniques to protect PLC circuits from hazardous overloads, transients, and ESD. In addition, this article provides electronic component recommendations for reducing PLC power consumption. Lower power consumption reduces the heat buildup in the PLC, which contributes to higher product reliability.
An Industry 4.0 system
Figure 1 illustrates the elements of an Industry 4.0 system. At the heart of the monitoring, control, and data-collection system is the PLC, which controls the system based on inputs from the factory floor. It transmits critical data on manufacturing processes, manufacturing tests, machine status, and quality control. The industrial IoT gateway transmits data, receives commands from a central command center, and then stores all data in the data center and the cloud.
Overview of a PLC
A PLC is a special-purpose computer optimized for monitoring and control operations. Because these computers operate in manufacturing environments with large, motorized equipment, warm temperatures, and manufacturing residue in the air, PLCs must be much more robust than general-purpose computers.
Figure 2 shows a general block diagram of a PLC. The table to the right of the block diagram lists the component types that can protect the PLC from hazards such as overcurrent conditions, high-voltage transients, and ESD. The table also includes components that can reduce the PLC’s power consumption. The following paragraphs present the need for each component in the specific circuit blocks and offer recommendations on their characteristics.
Protecting the PLC circuit blocks
Here are several recommendations to protect the PLC circuit blocks from overcurrent and transient voltages.
Power supply
The power supply converts the AC line voltage to 24 VDC, which operates the circuitry. The power supply is subject to current overloads and voltage transients on the AC line. Current overloads can come from surges on the AC line, and voltage transients can come from large motors turning on and off or lightning. Thus, the power supply requires current overload protection and protection from voltage transients.
A time-delay fuse will provide AC line current overload protection and avoid nuisance shutdowns due to current transients. Look for a voltage rating of at least 250 VAC for use on a 230-VAC power line. Also, ensure that the fuse has a current interrupting rating of at least 50 A. Select a fuse that complies with UL/CSA 248, Low-Voltage Fuses.
Absorb the high-voltage transients induced on the AC line using either a metal oxide varistor (MOV) or a protection thyristor-MOV combination to extend the MOV lifetime. Select an MOV that can withstand over 400 J of energy and absorb a surge current of up to 10,000 A. Be aware that some MOVs include an added protection feature. This thermal element protects the MOV by opening the connection to the leads if the MOV begins to overheat from an unusually large overvoltage.
Consider adding a protection thyristor in series with the MOV. The protection thyristor-MOV combination allows the selection of a lower-rated–voltage MOV and enables clamping the transient at a lower voltage. The protection thyristor, a crowbar-type device, responds to a transient overvoltage by turning on in nanoseconds. The protection combination has a lower leakage current than the MOV alone and increases end-product reliability and lifetime.
For optimum protection of sensitive semiconductors, please consider replacing the thyristor-MOV combination with a transient voltage suppressor (TVS) diode. Any portion of an overvoltage that passes through the MOV or the protection thyristor-MOV combination will be further absorbed and clamped at a low voltage. TVS diodes:
- Respond to transient voltages in a very fast time of under 1 ps
- Can safely absorb transient peak pulse power of up to 600 W
- Can safely absorb a surge current of up to 100 A
- Withstand ESD strikes of 30 kV
- Have unidirectional and bidirectional models
Use a polymer positive temperature coefficient (PPTC) resettable fuse for overcurrent protection of the power-factor correction (PFC) circuit in the power supply block. For many current ratings, these devices have low internal resistance (under 10 mΩ). PPTC fuses have fast trip times, typically under 5 seconds, and consume a minimum of PC board (PCB) space with surface-mount packages as small as the 0402 form factor.
The combination of a time-lag fuse, a series protection thyristor-MOV, and a TVS diode and PPTC fuse will ensure a thoroughly protected power supply circuit.
DC/DC converter
The DC/DC converter converts the 24 VDC to the voltages, typically 5 V and 3.3 V, required for the control and input-output circuit blocks. If 24 VDC directly powers the PLC, the DC/DC converter needs protection from overcurrent and transient conditions that can propagate on the unprotected 24-VDC line. For overcurrent protection, use a time-lag fuse compliant with IEC 60127-2, Miniature Fuses. Consider a surface-mount TVS diode to absorb and clamp transient voltages. Surface-mount versions can withstand peak pulse power as high as 3,000 W and peak surge currents of 300 A.
Input module
The input module converts the digital and analog input signals into levels and digitized values that the application processor can read. Because the input signals arrive from the external environment, they can carry hazardous transients. Use a TVS diode, either a bidirectional or unidirectional model, to protect the input module from a transient overvoltage. Models that can safely absorb 600 W of pulse power and 100 A of surge current provide suitable protection for the input module.
Protecting PLC circuit blocks from ESD
Display/user interface and wireless communication circuit blocks
The display/user interface and the wireless communication circuits interface with the external environment and can experience exposure to hazardous transients from ESD. The display/user interface has contact with operators, while the wireless communication antenna can attract ESD strikes from the outside environment.
Consider a TVS diode array consisting of two diodes connected anode to anode, as shown in Figure 3. This diode can withstand ESD strikes from direct contact of ±12 kV to protect touchscreen semiconductors in the display/user interface. This diode array also can protect the wireless communication circuit from through-the-air ESD strikes up to ±18 kV. In addition, this type of diode array has a low capacitance of under 0.1 pF to avoid performance degradation of wireless transmission and reception.
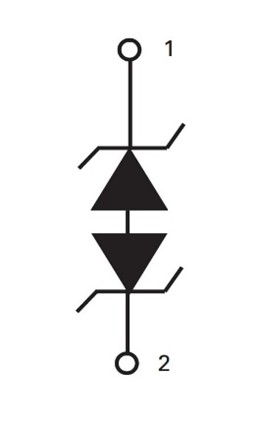
Figure 3: Schematic of an anode-to-anode TVS diode array for ESD protection (Source: Littelfuse Inc.)
An alternative to a TVS diode array for the wireless communication circuit is a polymer ESD (PESD) protection device. PESD components can withstand through-the-air ESD strikes of ±15 kV. They have low capacitance of 0.25 pF and typical leakage currents under 10 nA. Models of PESD components are available in the small 0402 surface-mount packages.
Wired communication circuit block
The wired communication circuit block also requires protection from ESD strikes. The recommended methodology depends on the communication protocol the PLC uses. For information on the protection of Ethernet, Power-over-Ethernet, USB, RS-232, and RS-485 communication ports, see the presentation “General Port Protection” at Littelfuse.com.
Maximize efficiency by reducing power consumption
In the power supply block’s switch-mode power supply, investigate Schottky barrier rectifiers to maximize efficiency and reduce power consumption. They enable fast switching, which allows more efficient high-frequency switch-mode supply circuits. Look for Schottky rectifiers with a low forward-voltage drop under 1 V, a low reverse current under 1 mA, and a dV/dt as high as 10,000 V/µs. Figure 4 shows a half-bridge Schottky diode pair with a common cathode connection. Use a dual-diode package to save PCB space.
The PFC circuit in the power supply block reduces the total current drawn by the PLC by keeping the voltage and current in phase with each other and by reducing current harmonics. Using an active PFC, a transistor acts as a switch to control current to an L-C network. Consider using a MOSFET. To maximize the efficiency of the PFC circuit, select a MOSFET with:
- A low RDS(on), with values under 150 mΩ
- A low gate charge, under 50 nC
- A dV/dt of at least 50 V/ns
These parameters enable efficient, low-power, fast switching.
In the PFC circuit, consider a SiC Schottky diode for greater efficiency. Schottky power diodes have low forward voltage, about 1.5 V, and pass currents as high as 8 A at high operating temperatures. This diode has a low leakage current, typically under 15 µA, and low recovery times for fast switching.
Optimizing control and maximizing reliability
Use a solid-state relay in the output module to drive actuators, motors, valves, and other devices. Consider an optically isolated relay with a low turn-on current of under 10 mA for reduced power consumption. Look for models with zero-voltage switching for minimum electromagnetic interference and radio-frequency interference. Also, look for optical isolation as high as 5,000 Vrms to ensure isolation and noise immunity between control and load circuits. Furthermore, solid-state relays contribute to high reliability with long life.
Realizing the benefits of Industry 4.0
It does not take many components to protect a PLC, improve its efficiency, and enhance its reliability. Fortunately, design engineers can take advantage of the component manufacturers to assist them with selecting appropriate protection and efficient control components for their PLC designs. Application engineers at the component manufacturers can:
- Help the designer select the most cost-effective components for protection and control
- Provide guidance on complying with applicable safety and performance standards for PLCs
- Perform pre-compliance testing (offered by some manufacturers) to help identify problems before standards compliance testing
Partnering with the component manufacturers can save design engineers significant development time and compliance testing costs. The result is a robust, reliable PLC that is both protected from overcurrent and transient voltages and more efficient. Such a PLC will enable the realization of the benefits of Industry 4.0.
References
- Littelfuse Inc. (2022). “Circuit Protection Products Selection Guide.”
- Littelfuse Inc. (2022). “Power Semiconductor Selection Guide.”
- Littelfuse Inc. (2022). “General Port Protection.”
About the authors
Prasad Tawade is a strategic marketing manager for the Electronics Business Unit of Littelfuse. His current responsibilities include managing go-to-market strategy for new products, developing monthly application spotlights and distribution marketing initiatives. Prasad joined Littelfuse in December 2018 during the acquisition of IXYS, where he was the EMEA distribution sales manager. Before IXYS, he worked as a product manager at Pericom Semiconductor and Cypress Semiconductor. Prasad holds a bachelor’s degree from Savitribai Phule Pune University (India) in electronic engineering and a master of engineering management degree from Duke University.
Simon Foley joined the IC Division of Littelfuse as a strategic marketing manager after holding the position of product marketing and BDM in the Semiconductor Business Unit. He started his 18-year tenure at Vishay, where he held several positions: application engineer, product marketing engineer, market development manager, through to business marketing director of the MOSFET and IC Business Unit. Simon’s electrical engineering experience began as a radar and telecoms engineer in the Royal Air Force, moving onto Concord Radio Altimeter System Engineering at British Airways. Simon has a mechatronics diploma and a computer architecture degree from Swansea Institute of Technology and the University of West of England.
Advertisement
Learn more about Littelfuse