Time is that precious, finite commodity that we are reluctant to watch, struggle to manage yet can ill afford to forget about. The usefulness of the innumerable electronic devices that assist us as we go about our daily lives is largely underpinned by their ability to keep track of “real” time i.e., the seconds, minutes, hours, days, and years we use to signpost our daily lives (Fig. 1).
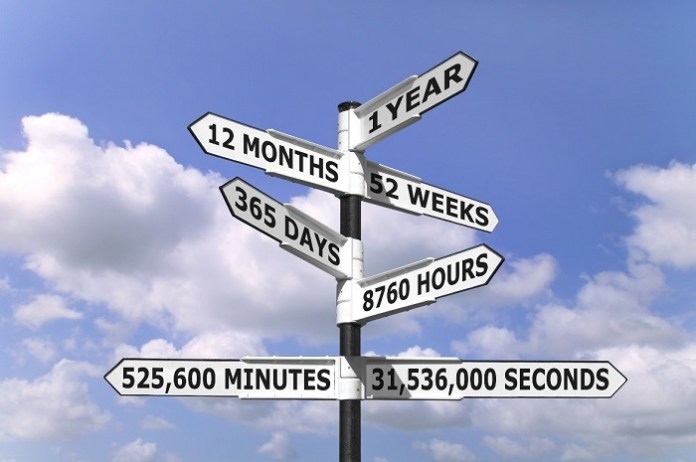
Fig. 1: Electronic devices must track real time.
Battery-powered portable, wearable, and IoT devices are faced with a much more disparate (and potentially extreme) set of operating and environmental conditions than static electronic equipment, which operate in predictable ambient conditions with the luxury of a permanent power supply. Whether sending up-to-date weather reports or calculating average calories burnt while exercising, IoT, and mobile devices rely on having the ability to keep track of time accurately and reliably even while potentially being subjected to vigorous physical movement in cold and damp, or hot and humid locations.
In this article, we show how these conditions can negatively impact the performance specifications of the crystal oscillator-based real-time clock (RTC), and present an RTC IC which combines greater timekeeping accuracy with increased robustness in applications where ruggedness performance is a must-have.
RTC operation
Most RTC ICs maintains time and date information by counting seconds, using a 1-Hz clock signal derived from the 32.768-kHz crystal oscillator, the standard timekeeping reference used by most electronic applications. The time and date information are stored in a set of registers, which is accessed through a communication interface, such as I2C. The crystal may be external to the IC or integrated within the same package.
Timekeeping accuracy, robustness/ruggedness, power, and size are the key specifications to consider when choosing an RTC. The relative importance of each has a bearing on the choice to select a standalone RTC IC or to use one already integrated into a system microcontroller, as we will discuss.
Timekeeping accuracy
The timekeeping of an RTC can only ever be as accurate as the timing reference it uses. Unfortunately, the typical 32.768-kHz tuning-fork crystal is not very accurate over a wide temperature range. Due to its parabolic characteristic (Fig. 2), this accuracy is typically ±20 ppm at room temperature (+25°C). This is the equivalent of gaining or losing 1.7 seconds of time each day, or 10.34 minutes per year.
As shown, accuracy decreases significantly at higher and lower temperatures. The typical accuracy at these temperatures is much worse than 150 ppm, which is the equivalent to losing almost 13.0 seconds of time each day, or over 1.3 hours per year.
Also, crystals are tuned to oscillate at the correct frequency under a particular capacitive load—using a crystal tuned for a 12.5-pF load on an RTC designed to present a 6-pF load to the crystal will cause the clock to run too fast. Careful board layout and assembly is required to minimize the effect of unwanted extra capacitance which can slow the clock. For RTCs with integrated capacitors, timing accuracy is limited by the manufacturing tolerances of the IC manufacturer.
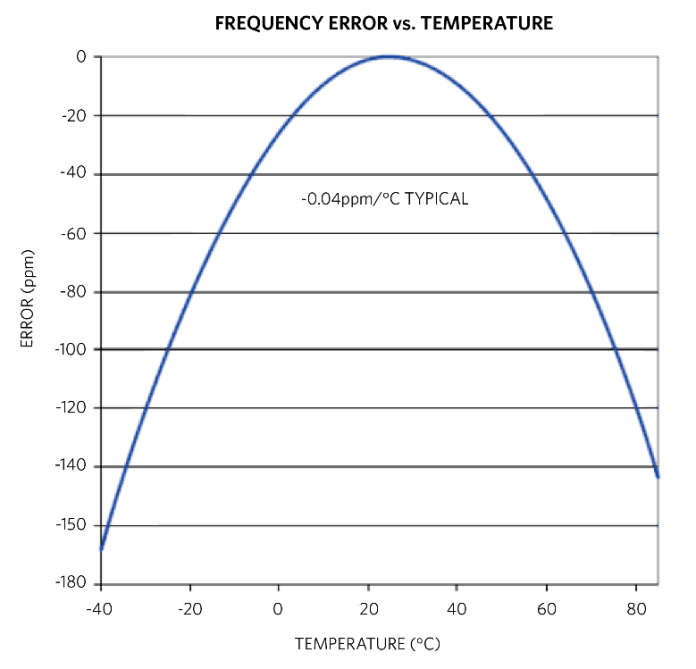
Fig. 2: Crystal accuracy v. temperature (Image: Maxim Integrated)
Robustness – shock and vibration
Mobile and portable equipment is regularly subjected to mechanical shock and vibration. Whether the vibrations experienced by a fitness tracker due to the movement of an exercising athlete or the G forces experienced by a piece of telemetry equipment dropping back to earth from a weather balloon (Fig. 3), each use case brings its own set of challenges.
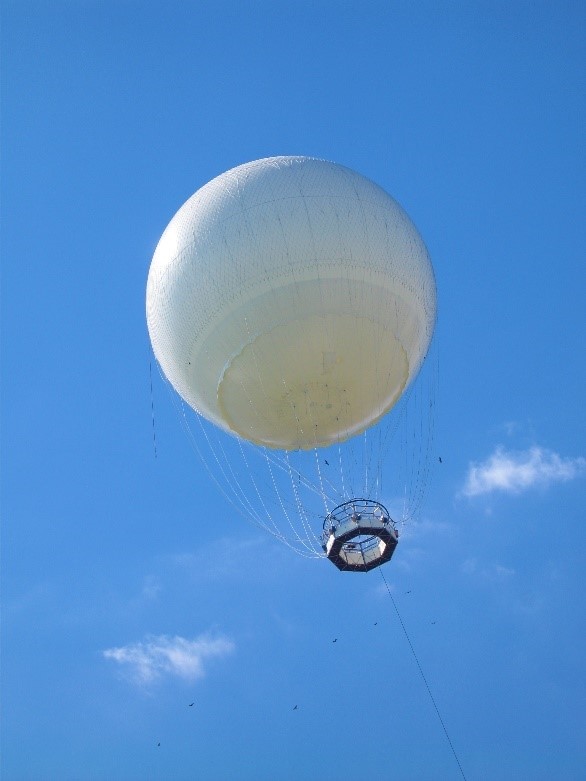
Fig. 3: Weather balloon
Crystal oscillators are relatively fragile, making them susceptible to damage by more extreme shock and vibration. Even when operating in more benign conditions, they lose accuracy simply due to aging at a rate of approximately ±1 ppm per year.
Ruggedness – temperature
During assembly, printed circuit boards are repeatedly subjected to high temperatures (reflow). This process can adversely affect the accuracy of an RTC. Fig. 4 shows the effect of a typical reflow operation (pre and post) on the performance of a crystal-based RTC, demonstrating a shift of up to 5 ppm.
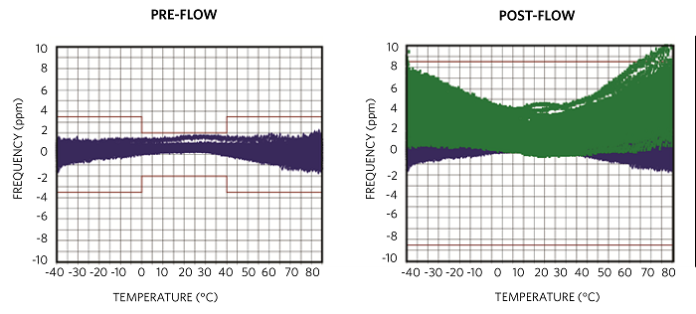
Fig. 4: Timing accuracy for a crystal based RTC pre- and post-reflow (Image: Maxim Integrated)
Current consumption and size
While current consumption and size are not directly correlated, they are interrelated. Many applications use a crystal oscillator-based RTC integrated within a system microcontroller. While this reduces the number of board ICs, it can have the unintended consequence of preventing the microcontroller from entering an ultra-low power “deep-sleep” mode.
For IoT devices not in continuous usage, e.g., a remote motion-detector camera that only wakes to transmit a picture when movement is detected (otherwise remaining in sleep-mode), this is important. Accurate timekeeping must be maintained, even when the device is not in use and a typical microcontroller can consume 60 0nA just to keep its RTC circuit awake, causing the device battery to drain more quickly.
It should also be noted that timekeeping accuracy is also determined by the microcontroller manufacturer. An external RTC IC-based solution provides the flexibility to design a potentially more accurate and lower power solution.
Balanced performance
Fig. 5 shows the functional block diagram of an RTC IC that strikes the best balance between all the functional requirements previously discussed.
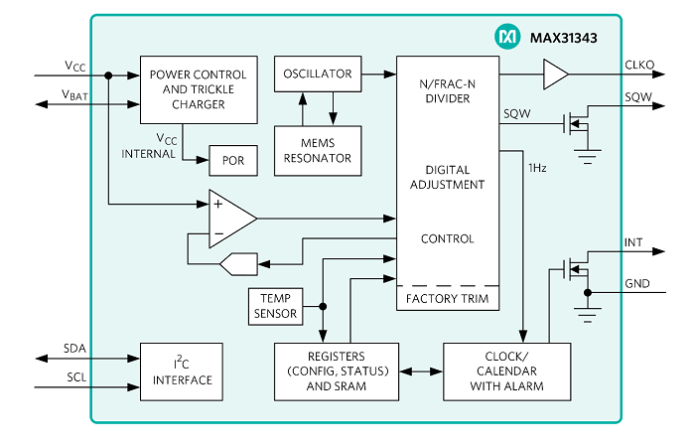
Fig. 5: MAX31343 RTC with integrated MEMS oscillator (Image: Maxim Integrated)
The MAX31343 IC uses an integrated MEMS resonator and oscillator which provide several advantages over crystal oscillator-based RTCs. With a time variation of only ±5 ppm (or ±0.432 second/day from -40°C to 85°C), it offers a 4× improvement in timekeeping accuracy with negligible variation (<±2 ppm due to aging or reflow during board soldering). It is also much more robust than crystal oscillator-based RTCs, with the ability to withstand mechanical shock (up to 2900 G; 5 shocks × 6 axes, JESD22-B104C Condition H) and vibration (with variable frequency of 20 G; 20/2000 Hz, JESD22-B103B Condition 1).
It allows serial data communication with a microcontroller via a bidirectional I2C bus. For additional redundancy, this RTC uses an integrated voltage reference and comparator circuit to monitor the status of VCC. This allows it to detect if a main system power failure is likely, allowing it to automatically switch to a backup supply (a rechargeable battery or supercapacitor) if required.
With a typical operating current of 940 nA, the MAX31343 can provide over five years of timekeeping from a BR1225 lithium backup battery rated at 48 mAh. An integrated trickle charger keeps the backup battery fully charged during normal operation.
Other useful features include two programmable time-of-day alarms, interrupt output, uncompensated programmable clock output, and a temperature-compensated programmable square-wave output. It is available in either 2.1 × 2.3 mm 8-Pin WLP or 4 × 3 mm 8-Pin TDFN packages and operates over a wide supply of 1.6 V to 5.5 V.
Summary
Battery-powered IoT, portable, and wearable electronic devices are expected to operate in widely varying environmental conditions with sufficient robustness to survive mechanical vibration and shock. These conditions can negatively impact the accuracy and performance of commonly used crystal oscillator-based RTC circuits, affecting their suitability for some applications.
An RTC IC that uses an integrated MEMS oscillator is shown to provide superior timekeeping accuracy which is negligibly affected by environmental conditions or mechanical shock and vibration. Consuming less than 1 µA in typical operation, it is suited for use in rugged applications including industrial sensors, action cameras, handheld instrumentation, and wearables.
About the Authors:
Binay Kumar Bajaj is a director, business management (Core Products Group) at Maxim Integrated. He has an MBA from Santa Clara University (Leavy school of Business) and B.S in Electrical Engineering.
Michael Jackson holds the position of principal technical writer at Maxim Integrated. He has a M.Eng. from Dublin City University.
Advertisement
Learn more about Maxim Integrated