Sensata Technologies recently introduced its Sensata IQ platform that enables factories to deploy plant-wide asset health monitoring to prevent unplanned downtime. The cloud-based platform uses artificial intelligence to process data from Sensata’s IoT devices (sensors and hardware) and qualified third-party sensors.
The solution targets the 85% of the plant’s assets that are typically unmonitored today. Online asset monitoring systems have traditionally been very costly and complex, resulting in many plants and factories monitoring only the most critical assets, said Bryan Siafakas, product line director of Sensata’s industrial sensing and IIoT portfolio, adding that they don’t use the cloud and are integrated into the control systems.
“Our focus is on the balance of plant assets where we don’t have to tie into the existing control infrastructure,” he said. “It is easily retrofittable on any asset that you might want to monitor in the plant.”
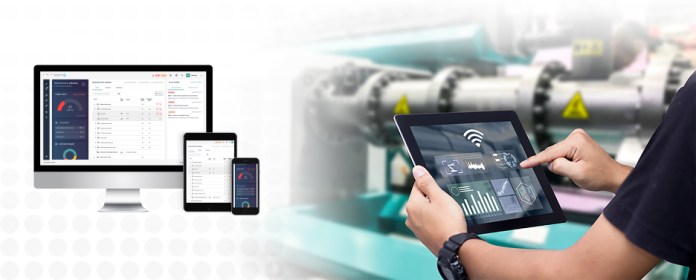
Factory managers and maintenance engineers can monitor all of their assets from anywhere, including on a smartphone, PC, or tablet. Click for a larger image. (Source: Sensata Technologies.)
The learning period to build a baseline of an asset takes about one or two weeks. That information is than stored and trended in Sensata IQ, leveraging AI and machine learning (ML), which is used to monitor for different types of faults.
“For certain assets and capabilities, we can do fault characterization and even remaining useful life,” said Siafakas.
For example, a user can be alerted to a fault on a fan with an estimated amount of time before the issue becomes disruptive to the process, he said. “We give context to the information and in many cases what the fault is that the user needs to address.”
Sensata estimates the solution’s fault characterization accuracy at 95% based on benchmarks.
“Accuracy is critical for these types of systems,” said Siafakas. “If you have a high number of false positives and maintenance personnel finds that there isn’t a problem, they’re going to lose trust in the system and they’re not going to use it. … So having data accuracy is very important to make sure that you have a very high degree of confidence when you characterize the fault.”
Some of the anomaly detection (via the sensors) is done on the edge, and when required, data is pushed to the cloud for more sophisticated analysis.
“We pushed the intelligence to the edge, where the sensor sits on an asset like a pump or a motor and samples it every 15 minutes, for instance,” explained Siafakas. “If it detects an issue, it will then transmit additional information, like a full waveform to the cloud when extra computational power is needed, for more sophisticated AI and ML analysis to characterize the fault. It really depends on what you are processing.”
The key point is to avoid downtime, interrupting the fault before it actually happens and brings a plant down, said Siafakas.
Easy to install and easy to use
Some key advantages of the system include easy installation, setup, and use, which is what Sensata calls a differentiator for its system. “It doesn’t require a broad skill set in software or analytics to be able to use it,” said Siafakas.
The ease of use starts with deploying Sensata’s sensors, which can be configured or installed with no tools. As an example, one of its wireless vibration sensors comes with a magnet mount, which can be placed on a motor or pump and configured with the Sensata IQ mobile app.
“Answer a few easy questions and then you can visualize it in the platform,” said Siafakas.
One of Sensata’s newest IoT sensors enables predictive maintenance for rotary assets with actionable insights for plant managers. Sensata said this solves the problem of existing solutions that do not provide real-time insights needed to monitor their assets.
The new wireless 6VW series IoT sensor solution monitors rotary assets using a multi-modal sensor and AI-driven algorithms and analysis capabilities from Nanoprecise, a technology partner. The data from the sensor is analyzed at the edge for anomalies, delivering insights to Sensata IQ for further analysis and data visualization. The platform uses the data to identify potential faults, calculate projected remaining useful life, and deliver alerts.
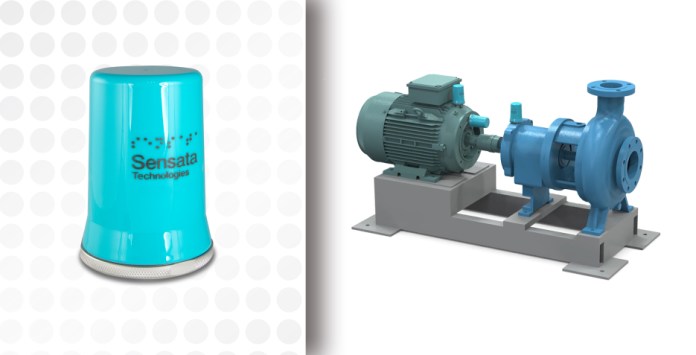
Sensata’s wireless 6VW multi-model IoT sensors allows plant managers to detect early-stage faults in rotary machine assets. Click for a larger image. (Source: Sensata Technologies)
The 6VW is a self-install solution with a mobile app for device configuration, making setup and installation possible in less than five minutes, according to the company. The solution can simultaneously monitor each asset using six sensing modalities: vibration, temperature, acoustic emission, speed, humidity, and magnetic flux. The sensors can be retrofitted into a range of existing rotary assets such as motors, pumps, blowers, fans, or compressors, regardless of brand or manufacturer, without requiring changes to a company’s hardware or control platforms.
“What also makes Sensata IQ easy to use is that AI and ML takes the domain expertise required from the customer and packages it into models that are running in the system,” said Siafakas. “AI allows the system to take on that domain expertise so the maintenance manager or plant management can interpret those signals in an easy way, alerting them that there will be an anomaly or particular fault in the system.”
The alerts are configurable. Users can input their own alarm thresholds or use machine learning to trigger those alerts, said Siafakas, which are sent via text message or email or to the dashboard. User roles can also be assigned.
For ease of use, factory managers and maintenance engineers can monitor all of their assets from anywhere, including on a smartphone, PC, or tablet. They also receive alerts regarding the equipment’s health before assets fail. This reduces unplanned downtime and optimizes maintenance strategies.
There are many benefits to avoiding downtime, said Siafakas. These include “the financial impact, which for many manufacturers can be in the millions of dollars per year, as well as spare parts optimization, ensuring that the right parts are on hand, and actually planning maintenance around a specific time window instead of reacting to assets that are failing.”
The sweet spot for the Sensata IQ solution is factories and buildings that use “a lot of rotating equipment, such as pumps, motors, compressors, fans, and gearboxes and for anyone interested in reducing downtime and improving efficiency,” said Siafakas.
Advertisement