As part of a complete flow sensing solution, Flusso, a fabless semiconductor company spun-out from the University of Cambridge, has claimed the industry’s smallest flow sensor for use in high-volume consumer and industrial markets. The FLS110 flow sensor, measuring 3.5 x 3.5 mm, is small enough to fit into any product and can be placed close to the where the measurements are needed, said the company.
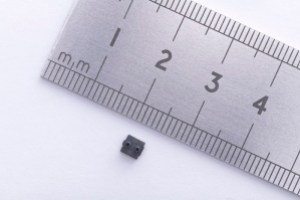
Flusso’s FLS110 flow sensor in a 3.5 x 3.5 mm package size measures flow rates from as low as 0.001 to over 500 slm, to meet a broad range of application requirements. (Image: Flusso) Click for larger image.
The flow sensor measures flow rate across a wide measurement range of 0.001 to over 500 standard liters per minute (slm, in a bypass configuration), offers repeatability of 0.5 standard cubic centimeters per minute (sccm) +0.5%, and delivers a temperature-compensated flow signal.
Flusso’s patented technology, based on a CMOS MEMS silicon platform developed at the University of Cambridge, UK, enables flow sensors to be made significantly smaller and less expensive than traditional flow sensors. This enables them to be used in applications that were not previously possible due to size, cost, and integration challenges, said the company.
Flusso was founded in 2016 by Professor Florin Udrea (co-founder of CamSemi, Cambridge CMOS Sensors, Cambridge Microelectronics, and Cambridge GaN Devices), Professor Julian Gardner (co-founder of Cambridge CMOS Sensors and Sorex), Dr. John Coull, and Dr. Andrea De Luca.
De Luca, who is also CEO, was awarded a Young Engineer of the Year Award by The Royal Academy of Engineering for his pioneering work in MEMS sensor development.
In February 2020, the company raised $5.7 million Series A funding to ramp up production of the FLS110 flow sensor.
The flow sensing solution
Flusso’s product is more than a flow sensor. It is a flow sensing solution that comes with a complete design package and application engineering support to help product manufacturers incorporate flow measurement into any product or system for the first time. New use cases targeted range from detecting pipe blockages in industrial systems and smart air management for smart buildings to active filter monitoring in consumer appliances such as vacuum cleaners and air-conditioning units and smaller and lower cost sensing for home health-care products such as smart inhalers and fitness monitoring masks.
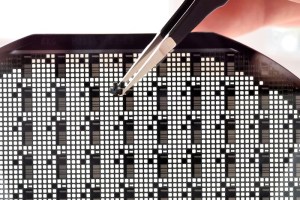
The FLS110 is a CMOS MEMS sensor that has been developed from Flusso’s patented sensing platform on a silicon CMOS wafer, where each transparent ‘window’ is a single sensor on an etched membrane. (Image: Flusso) Click for larger image.
Flusso built the product around a silicon CMOS process developed at the university. But having only the silicon sensors was not enough, De Luca told Electronic Products. “The package is extremely important together with everything else that you have around it in terms of the electronics, the software, and firmware to make the electronics work as well as the mechanical and fluidic integration, which are all extremely important for flow sensing.”
It’s not unique to have a flow sensor based on MEMS technology, but some of the CMOS processes as well as Flusso’s approach to designing flow sensors are different from traditional methods, explained De Luca. But it’s not only the processes, it’s also the materials used and, of course, the design of the sensors, he added.
“We try to match our initial aspiration of targeting high-volume consumer and low-cost type of markets with packaging concepts that the normal microelectronics packaging house could actually manufacture in very high volume and low cost by taking advantage of the batch-type fabrication processes and adapting those in a sort of modular way to the flow sensor,” said De Luca. “We try to make a sensor, which is extremely small to cut costs and also to enable applications that were not serviced before. We put a lot of effort into making sure that this miniaturization of the package would not affect the performance of the flow sensor itself.”
So there is a lot of novelties in how these processes and packaging materials are put all together with the design aspect as well as the fluidics – everything that is related to the fluid moving into the package, he added.
Customization
What makes the FLS110 flow sensing solution different is that it is ‘fully’ customizable, said Flusso, unlike traditional flow sensors with limited customization and their own processing circuitry to implement functions and algorithms that are normally inaccessible to their users. The solution package includes software that allows users to configure and customize different operating modes of the flow sensor.
“What makes our offering different from what other people are doing is the fact that we try to build into our proposition a level of flexibility that other flow sensors don’t have,” said De Luca. “We offer not only a flow sensor component, but also the firmware or software as part of the of the solution itself.”
In addition, the sensor works with an external microcontroller, which can either be dedicated to the sensor itself or a general microcontroller used for other purposes. The firmware for the MCU has built-in flexibility that enables the users to balance or tradeoff performance with system costs. Firmware includes sensor control, sensor reading, temperature compensation, along with other algorithms.
Performance tradeoffs include specifications that can impact power consumption and noise (such as repeatability or accuracy). In addition, customers also have flexibility in terms of the mechanical and fluidic aspects and the choice of microcontroller, which both have an influence on performance and cost, explained De Luca.
This kind of flexibility is not available with traditional solutions that often use an ASIC and electronics integrated with the sensor, which offers very little customization, according to De Luca.
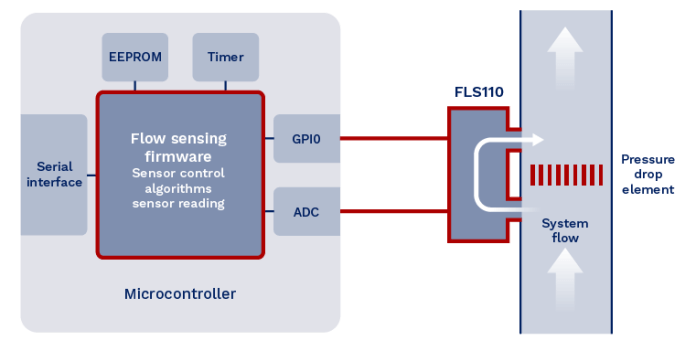
Flusso provides the flow sensor along with full solution (noted in red). (Image: Flusso)
If customers want to sense a specific range, they need to design a pressure drop element with these characteristics into their systems, said De Luca. “If they do that our component is compatible with their design and the solution will do the same job as a flow meter set for that range.”
This gives them two advantages, he added. “We have one component that can cover different ranges and the pressure drop element that they designed enables it to nicely integrate with their system, which gives them a degree of flexibility because they don’t have to adapt their design to the design of the flow sensor.”
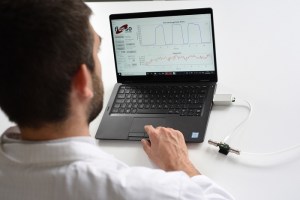
Customers can measure and log the sensor output within their own application with the FLS110 evaluation kit. (Image: Flusso) Click for larger image.
What about the learning curve using this approach? De Luca said the evaluation kit gives them everything they need to play around with the different settings via a graphic interface – sensor, microcontroller, other electronics, firmware, and fluidic fixtures to select flow range. It plugs right into the customer’s flow system with push-fit connectors and works with a PC via a USB adapter to view and record sensor data.
Flusso offers a variety of fluidic fixtures (which makes it easier to integrate into an existing system) to accommodate a range of different flow rates and pressure drops. The company provides the pressure drop – flow rate characteristics for each fixture to help customers select the right one.
“After they go through the evaluation phase of their projects, it actually doesn’t require too much of an extra effort because all of the main information will come from us,” said De Luca. “We will tell them that the analog sensors require a PCB with this footprint and connection to the microcontroller, so we give them this part of the design, and all of the firmware is coming from us, so they don’t need a software engineer or a firmware engineer to design it. We can also advise them on the fluidic and mechanical integration during the product integration phase.”
Customers get access to a full package of electronic, mechanical, and fluidic engineering know-how and support to incorporate flow measurement into their products. This allows customers to decide for themselves the right balance of performance versus cost. The package includes flow sensing firmware, software to configure and customize different FLS110 operating modes depending on the application requirements, design guides, and application engineering support to help shorten new product development.
The FLS110, housed in a 6-pin DFN package, is reflow solderable and shipped in tape and reel for automated product assembly. Samples are available now in the evaluation kit. Volume production will start in the first half of 2021.
Advertisement
Learn more about Flusso