In the rapidly evolving landscape of embedded systems, the demand for precise, efficient and real-time control applications continues to surge. Microcontrollers (MCUs) continue to be a critical component in these applications, serving a broad spectrum of sectors, such as automotive, consumer electronics, healthcare, aerospace and industrial automation.
As technology evolves, compact yet powerful MCUs are undergoing significant transformations to meet the ever-increasing demands of the industry. This evolution is characterized by several key trends that are shaping the future of MCU technology and driving the need for a higher-performance MCU with advanced peripherals to perform accurate and precise measurements, all while making adoption easy with a complete development ecosystem.
The imperative for enhanced performance
Modern MCUs address a range of challenges, from increased software complexities to the need for improved energy efficiency. They also provide integrated peripherals for multifunctional capabilities and meet strict safety and security standards. The following section delves into the specifics of these advancements, highlighting their role in transforming the potential of MCUs within the digital landscape, which requires higher performance from today’s MCUs.
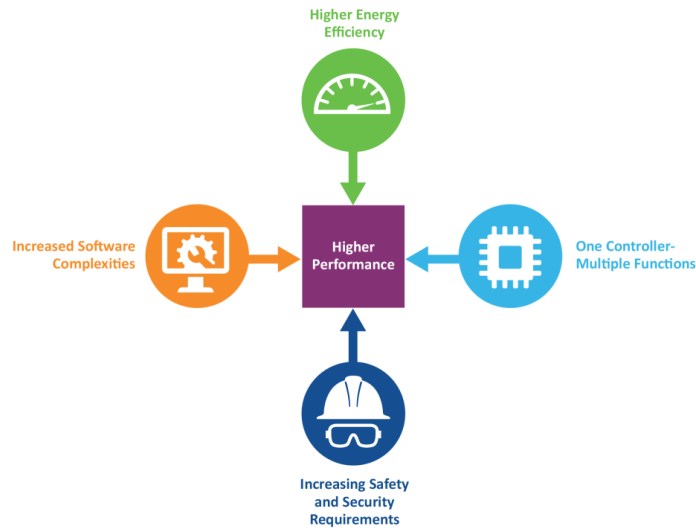
Figure 1: MCUs address a range of challenges, from increased software complexities to the need for improved energy efficiency. (Source: Microchip Technology Inc.)
Increased software complexities
- Model-based design integration: MCUs now facilitate rapid prototyping and code generation through model-based design tools, expediting complex software development and market readiness.
- Robust safety and security: Enhanced MCUs feature comprehensive ecosystems with cryptographic modules, secure boot and fault-tolerant architectures to ensure system integrity. MCUs must also have the processing power to run functional safety diagnostics and security functions together with the main application functions.
- Advanced memory and processing: To meet growing software needs, MCUs boast larger memory and greater processing power, supporting complex applications and multitasking.
Higher energy efficiency
MCUs are increasingly designed with advanced features to enhance system energy efficiency. This includes the integration of innovative—and faster—analog peripherals, enhanced architectures for code efficiency and higher performance, enabling the design of efficient systems to control motors, power supplies and charging systems that consume less power without compromising performance.
Additionally, sophisticated algorithms are embedded within MCUs to manage and optimize energy use dynamically, to help ensure peak system performance with minimal energy consumption. These improvements contribute to longer battery life in portable devices, reduced conversion loss and lower energy costs in various applications.
One controller, multiple functions
- Multifunctionality: Serve as all-in-one devices, enabling synchronized function management
- Streamlined architecture: Simplify system design, minimize extra components and enhance performance
- Integrated peripherals: Save PCB space, reduce system costs and contribute to high-speed operation
- Compact and cost-effective: Facilitate the creation of small, economical, yet potent electronic systems
Increasing safety and security requirements
- Safety compliance: Modern MCUs cater to automotive, industrial and consumer sectors, embedding safety features to meet ISO 26262, IEC 61508, IEC 60730 and other standards. They boast fault tolerance, error correction and self-testing to mitigate system failures and enhance user safety.
- Security enhancements: To combat cyber threats, MCUs incorporate cryptographic accelerators, secure boot and secure access control to protect data and intellectual property.
This means, beyond operating the primary application, MCUs are now required to execute supplementary security- and safety-related functions. This demands increased CPU bandwidth, thereby necessitating enhanced performance from the MCU.
High-performance digital signal controllers
Within the domain of applications served by embedded systems, real-time control applications necessitate rapid, deterministic responses for effective operations. Advanced MCUs equipped with DSP capabilities are essential for high-speed, low-latency processing of complex algorithms and are critical for real-time applications, such as motor control, power conversion and sensor interfacing, where timely and precise system responses are necessary. Microchip Technology’s dsPIC digital signal controllers (DSCs), for example, have emerged as a popular solution, addressing the intricate needs of real-time control with high precision and reliability.
Unveiling the new, advanced dsPIC33A series
In response to market trends, driving demand for higher performance, Microchip has introduced its next-generation dsPIC DSC with several key enhancements. This evolution encompasses the integration of superior performance capabilities, expanded memory in future devices and advanced and faster peripherals, alongside the implementation of advanced security and safety features, to effectively meet and address market requirements and challenges.
The following image (Figure 2) shows the evolution of Microchip’s dsPIC DSCs, including the new dsPIC33A series, the fifth generation of digital signal controllers from Microchip.
The dsPIC33A DSC series is a groundbreaking advancement in MCU technology, offering a robust and efficient platform that excels in memory management, execution optimization and functional safety support. With its unified memory architecture, high-performance 32-bit CPU, double-precision floating-point unit (DP-FPU) and other advanced features, such as high-speed peripherals and comprehensive safety measures, this developer-friendly series suits a wide range of applications, ensuring precise, real-time control and the ability to tackle complex tasks.
32-bit CPU
The dsPIC33A introduces a 32-bit, 200-MHz CPU with a DP-FPU, enhancing performance and design for digital power and motor control applications. It simplifies model-based designs and third-party tool integration, increasing accuracy and development speed.
DP-FPU
This unit is IEEE 754-2019–compliant, supporting single and double precision with a dedicated pipeline, improving software reliability and control loop speed while reducing software errors associated with variable scaling. It includes hardware-based sine and cosine functions for better motor control.
Enhanced DSP engine and CPU
Features include two 72-bit accumulators for high resolution and accuracy with a significantly lower risk of overflows or underflows in results. The 32-bit working registers offer high performance and resolution and minimize the need for variable scaling, decreasing the likelihood of overflows or underflows. The seven context-switching registers minimize latency in real-time applications.
Advanced high-speed peripherals
The dsPIC33A boasts a 12-bit ADC with 40 MSPS, operational amplifiers with 100-MHz gain-bandwidth product and fast comparators with 5-ns response time, enhancing performance and reducing latency for motor control, digital power conversion, advanced sensor interfacing and other real-time applications.
Moreover, specialized peripherals, such as quadrature encoder interface and bidirectional serial synchronous interface, facilitate real-time tracking and data exchange for rotating shaft positions without disrupting the data stream. Core-independent peripherals, such as configurable logic cells and peripheral trigger generators, optimize CPU efficiency by handling tasks autonomously, allowing the CPU to focus on more critical operations.
Enhanced security features and memory architecture
Security is bolstered with an immutable root of trust, secure debug and flash segment access restriction. Error-correction code on all memory, performance monitoring and improved clock monitoring enhance safety. A unified memory architecture and dual RAM banks optimize performance and simplify direct memory access.
Simplified development ecosystem
The new dsPIC33A series streamlines embedded system development with its model-based design, and the instruction set architecture is compatible with existing dsPIC33 DSCs for a smooth transition. It integrates effortlessly with the MPLAB XC-DSC compiler and MPLAB code configurator.
The series is supported by the dsPIC33A Curiosity development board (EV74H48A), featuring modules tailored for motor control, digital power and other embedded applications. The ecosystem will soon grow to improve support for model-based design, motor control and DSP algorithms for advanced sensing, digital power and other applications, as well as to boost functional safety.
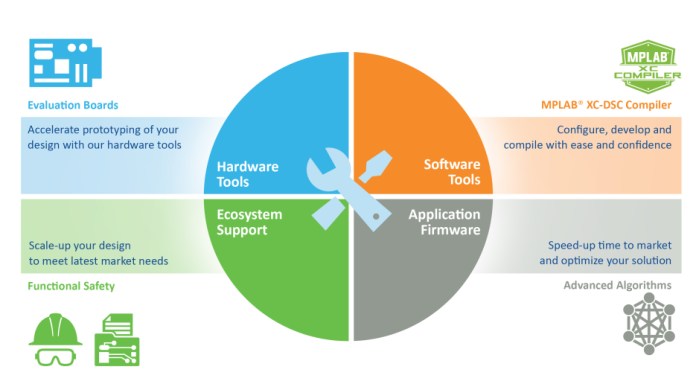
Figure 4: Microchip’s development platform for MCUs, MPUs and DSCs (Source: Microchip Technology Inc.)
Applications and markets
The new dsPIC33A family of DSCs will help enhance the performance of a range of real-time control applications across industries:
- Motor control: Whether in industrial automation, automotive systems or robotics, dsPIC DSCs deliver precise motor control, enabling smooth and efficient operation.
- Power electronics: In power electronics applications, such as inverters, converters and power supplies, dsPIC DSCs play a vital role in achieving accurate control and regulation of electrical power.
- Sensor interfacing: Real-time processing of sensor data is vital in applications such as instrumentation and monitoring. dsPIC DSCs efficiently handle data from various sensors, ensuring fast and accurate responses leveraging its high-performance core and advanced high-speed analog peripherals.
First product in the dsPIC33A DSC family
The first family of dsPIC33AK128MC1xx DSCs will include 128-kB flash and an extensive peripheral set and will be offered in various packages, including SSOP, VQFN and TQFP options ranging from 28 to 64 pins, with package dimensions as small as 4 × 4 mm. Future dsPIC33A families with additional memory, peripherals and larger pin counts will complete the portfolio.
The dsPIC33A DSC is a game-changer for developers of embedded systems in the automotive, industrial and consumer sectors, representing a fundamental shift in real-time control strategies. With its advanced core, comprehensive peripherals and versatile development tools, the dsPIC33A DSC helps engineers develop complex control algorithms that address the escalating needs for performance, safety and efficiency.
About the author
Pramit Nandy is a product marketing manager at Microchip Technology, focused on motor control applications. Nandy has been with Microchip since 2021, and his previous experience includes product marketing manager at onsemi, analog system design engineer at NXP and control system engineer at various other companies. He holds a master’s degree in electrical engineering from Arizona State University, complemented by a Bachelor of Technology degree in instrumentation and control engineering from the College of Engineering Pune Technological University, India. With a professional background spanning over 16 years, across multiple countries, Nandy has cultivated a deep expertise in electrical systems and control engineering.
Throughout his career, Nandy has honed his skills across a spectrum of technical positions, including analog system design engineer, system architect, application engineer and control system engineer. This diverse experience has provided him with a comprehensive understanding of system design and its practical applications across multiple sectors, such as automotive, industrial, telecom, cloud power and consumer markets. As a strategic thinker and a dedicated professional, Nandy continues to drive growth and success for motor control applications at Microchip Technology.
Advertisement
Learn more about Microchip Technology