Presence-detection solutions are not “one size fits all.” The core sensors and technologies required to accomplish the variety of features and use cases are as diverse as the applications and environments in which they are used. This series of articles on presence detection will feature examples of use cases across commercial, industrial, and retail applications and will highlight core sensing capabilities, networking and processing considerations, and technology solutions that can be architected together to achieve the desired feature set.
In each case, system architectures must take into consideration environmental factors; the shape, structure, and layout of the space; power availability; node-to-node communications requirements and constraints; and data and information security. STMicroelectronics previously covered social distancing in retail applications and presence detection for commercial building automation. The third installment (below) focuses on social distancing in the supply chain.
It goes without saying that 2020 has brought about a significant shift in our habits and behaviors. This has been reflected in every single aspect of our lives. In a matter of weeks, the entire world was housebound, with little visibility into when any semblance of normal life would resume. In many countries, people were required to have government-issued passes to even leave their homes to go to work or to shop for basic necessities.
The impact to the supply chain was swift and severe. Within days, consumers were in panic mode and began hoarding everything from food to paper goods and even board games and exercise equipment. Who could forget the rows of barren shelves where toilet paper used to reside, or the empty refrigerated meat units?
With shops closed, people turned to online shopping for essentials as well as emotional comfort, putting a strain on warehouse employees. Many people also sought both sustenance and comfort in cooking, not only because restaurants were closed but because they were housebound and stressed.
Meanwhile, the coronavirus spread through food-processing facilities and warehouses like wildfire. Workers who were once considered “behind the scenes” became frontline, essential personnel overnight. Even with the appropriate personal protective equipment (PPE), the virus was spreading because of the close contact that workers have with each other and with objects and surfaces that others had touched.
There are numerous laws and regulations that dictate the safety standards and protocols that must be followed in manufacturing and warehouse facilities. Typically, these regulations have focused on clear, immediate threats to safety such as moving equipment and fall hazards.
Factories and warehouse employers now must accept that contagion mitigation will be a permanent requirement of workplace safety, even after we emerge from the throes of the coronavirus pandemic. At a minimum, technologies that promote and enforce social distancing will be vital to ensure that workers can safely perform their tasks while minimizing the risk of infection. Additionally, technologies that automatically log contact-tracing information will help contain risks and can prevent outbreaks that would otherwise force the entire facility to shut down.
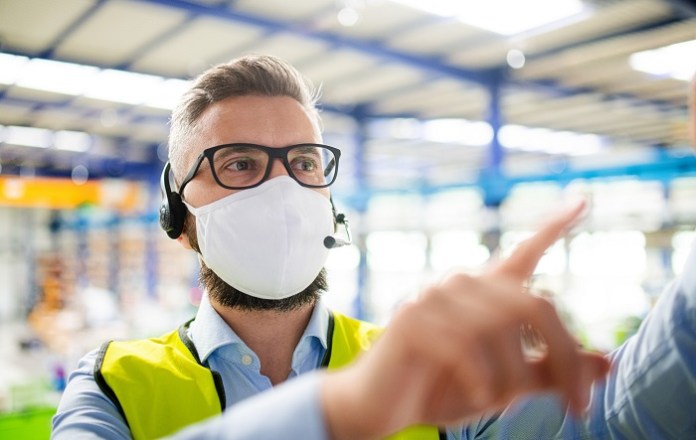
PPE, in combination with technologies that promote social distancing and remote and touchless interactions between people and equipment, offers the best way to maintain high productivity while keeping workers safe from infectious diseases. (Image: Shutterstock)
Presence detection in factories pre-pandemic
Before the pandemic, presence-detection solutions existed in factories for one primary purpose: to ensure the safety of interaction between automated equipment, or the facility itself, with the person operating the equipment. These systems were often deployed in a fairly rudimentary fashion. For instance, it is common to create a safety perimeter around a moving piece of equipment by placing floor pads equipped with pressure sensors around the machinery. When a person steps on the pad, their weight triggers the equipment to shut off because they have breached the safety perimeter.
Similarly, basic forms of obstruction detection are often used to shut down translating, rotating, or cutting equipment in the event that a person’s extremity or limb gets too close to a hazardous zone. These are often implemented using a simple motion detector, such as a passive infrared or low-grade radar. Some more sophisticated solutions involve object recognition, such that a hand or arm can be positively identified. These products often use camera-based technologies to achieve true object imaging.
Although not widely implemented, facial recognition or facial authentication is also sometimes deployed in order to validate that specific personnel were qualified to operate the various machinery within the factory. Most typically, equipment access verification is implemented via security badges or access codes. Clearly, these methods are not foolproof and can be circumnavigated with little difficulty.
Nearly all current forms of presence detection are isolated and instantaneous; that is, the detection event is used to trigger a response from the machine and is not transmitted, logged, or recorded beyond the singular instance. Additionally, these solutions are intended to ensure safe interaction between humans and machinery. Solutions to ensure safe interaction among the workforce personnel is not as widely available or adopted in current industrial automation methodologies.
Presence detection and social-distancing PPE in factories during a pandemic
Equipping an industrial facility with facility-based presence-detection solutions is beneficial for traditional safety and security concerns and can assist with social distancing and contagion mitigation in a general occupancy sense. These solutions and their benefits were broadly discussed in a prior installation of this series (see “Intelligent presence detection for commercial building automation”).
Adding touchless interaction with machinery, either through speech recognition or facial authentication, can be beneficial in terms of contagion mitigation by limiting a person’s need to touch a potentially infectious surface. However, in order to facilitate productivity in environments that typically require high degrees of physical labor and, often, physical interaction between employees and with operating equipment, a dedicated solution must be considered.
It is possible to deploy such a solution using only equipment that can be outfitted around the facility, that is, without requiring some type of wearable device for each employee. However, such a solution would need to be quite sophisticated, requiring highly accurate facial-recognition technologies. This type of equipment is likely to be cost-prohibitive, particularly given the number of edge nodes that would be required for deployment around a large facility, as well as the amount of data that would be collected, transmitted, and processed.
Wearable technologies equipped with Bluetooth Low Energy (BLE) provide the most comprehensive solution for both real-time social-distancing enforcement and automated contact tracing. Each device emits a BLE signal, and the strength of the signal can be used to calculate the proximity between devices. This is effective for a number of use cases. Primarily, it can be used to alert two employees when they are within an unsafe distance from each other, and in that way, it can decrease the risk of contact transmission in the workplace environment.
It may also be prudent to trace surfaces and touchpoints around the facility that are potentially infectious as well. This can be achieved by equipping BLE beacons around the facility as well, creating a “map” of each person’s movements and potential surface interactions throughout the facility. Embedded edge processing can provide first-level signal and data filtering, as well as manage data transmission.
In order to create a database of interactions with both people and facility surfaces, the data must be transmitted to a centralized data server. This is an obvious requirement for mapping an employee’s movements throughout the facility, but it is also required to create a contact-tracing database. As industrial facilities resume capacity operations, it will be inevitable that workers will engage with each other, particularly for functions that require multiple employees to accomplish a physical task. In these cases, automated contact tracing will be necessary to contain outbreaks that threaten the health and wellbeing of all of the employees and have the potential to shut down an entire facility.
This requires additional connectivity technologies from the BLE nodes (wearable or building-based). These devices could easily transmit their data to existing building gateways through the current RF protocol used by the other building automation systems or any other wireless protocol that is implemented.
Additional considerations for this type of system are described in this ST Reference Design for Wearable Social Distancing Technology. This publication also references use of an accelerometer to reduce overall power consumption, although in some cases, the use of an accelerometer for a low-power state may not be advisable, as one would want their device to continue to transmit its BLE signal even if the person is stationary.
PPE enhancements for social-distancing productivity
As workers return to full capacity in industrial settings, they must be equipped with the proper tools and PPE to maintain their efficiency while protecting their health. From an inter-employee communication standpoint, this can easily be achieved with more widespread adoption of headsets, radios, and other PPE that allow for remote communication. Advanced microphone and audio processing technologies make these solutions suitable for even the noisiest environments.
These devices could be further augmented with embedded speech-recognition technologies, which could provide numerous benefits. By deploying embedded speech recognition, the employee would be able to perform many routine equipment interactions by audible command, reducing the potential that they must touch common surfaces and potentially spread infectious material. It also has the added benefit of potentially increasing productivity and efficiency.
The future of workplace safety: Automated solutions for safe and healthy environments
By applying the practices of industrial automation and industrial IoT (IIoT) to industrial workers, manufacturing and supply-chain companies can ensure the health and safety of their staff even amidst a global pandemic. As we enter a critical period of the coronavirus pandemic across the globe, employers must find ways to mitigate the risks associated with working in an environment that requires physical presence to get the job done.
Technologies that promote social distancing and remote and touchless interactions between people and equipment offer the best way to maintain high productivity while keeping workers safe from infectious diseases. Many factory and warehouse employees already use wireless radios and headsets to communicate to each other across the facility, and as social-distancing measures are increasingly enforced, these will become a necessary form of PPE.
By adding automated contact-tracing capabilities to standard PPE, factories and warehouses can ensure the ongoing productivity of their facilities and reduce the risk of an infectious outbreak that not only endangers their employees but forces their facilities to lose productivity or even shut down.
Related articles:
Part 1: Automated presence detection for social distancing in retail applications
Part 2: Intelligent presence detection for commercial building automation
Advertisement
Learn more about STMicroelectronics